당신은 주제를 찾고 있습니까 “반도체 테스트 공정 – 반도체 테스트 공정, 6분만에 이해시켜드립니다!!“? 다음 카테고리의 웹사이트 https://you.charoenmotorcycles.com 에서 귀하의 모든 질문에 답변해 드립니다: https://you.charoenmotorcycles.com/blog. 바로 아래에서 답을 찾을 수 있습니다. 작성자 주모남TV 이(가) 작성한 기사에는 조회수 6,557회 및 좋아요 107개 개의 좋아요가 있습니다.
반도체 테스트 공정 주제에 대한 동영상 보기
여기에서 이 주제에 대한 비디오를 시청하십시오. 주의 깊게 살펴보고 읽고 있는 내용에 대한 피드백을 제공하세요!
d여기에서 반도체 테스트 공정, 6분만에 이해시켜드립니다!! – 반도체 테스트 공정 주제에 대한 세부정보를 참조하세요
반도체 후공정 테스트 공정, 이건 아셔야 사업보고서 읽기 편하십니다.
기업 조사전에 가장 기본적인, 테스트 공정 같이 공부해봐요.
6분만 투자하시면 됩니다!!
#반도체후공정 #테스트공정 #6분투자
반도체 테스트 공정 주제에 대한 자세한 내용은 여기를 참조하세요.
[반도체 특강] 테스트(Test), 반도체의 멀티 플레이어
반도체 후공정에서 이뤄지는 테스트(Test)란, 전기적 특성(Electrical Characteristics) 검사를 통해 칩(Chip)의 불량이 다음 공정으로 넘어가지 …
Source: news.skhynix.co.kr
Date Published: 8/22/2021
View: 9561
반도체 TEST공정 – 코딩게임
반도체 테스트는 불량칩을 골라내고 앞서 진행한 공정을 점검/개선하는 것이다. 해당 과정에서 다음 공정으로 불량 칩이 넘어가지 못하게 하는 선별률( …
Source: slaks1005.tistory.com
Date Published: 4/8/2022
View: 4062
[반도체 공정] 반도체? 이 정도는 알고 가야지:(8) Wafer test …
Wafer TEST공정은 웨이퍼 상태에서 여러가지의 검사를 통해 각 칩들의 상태를 확인하는 과정을 말합니다. 지난 컨텐츠에서 살펴 본 공정과 최종적인 제품 …
Source: www.skcareersjournal.com
Date Published: 10/15/2021
View: 7155
반도체 패키지 테스트 공정 관련 국내 기업 – 세상 쉬운 주식
반도체를 테스트 장비(Tester)에 넣고 다양한 조건의 전압, 전기신호, 온도, 습도 등을 가하면서, 반도체가 해당 조건별로 어떤 전기적 특성, 기능적 특성 …
Source: seshiju.tistory.com
Date Published: 5/27/2021
View: 5159
[반도체 8대 공정] 8탄, 완벽한 반도체로 태어나기 위한 첫 번째 …
수많은 제조공정을 거친 반도체 칩은 마지막 절차인 테스트를 통해 양품, 불량품을 선별하게 됩니다. 반도체 제조과정에서는 다양한 테스트가 …
Source: www.samsungsemiconstory.com
Date Published: 3/27/2022
View: 4772
[반도체 공부] 후공정(test & package)
[반도체 후공정]. Packaging(Assembly), Test 공정을 후 공정이라 한다. 반도체 칩, 즉 집적회로(IC)를 기판이나 전자기기의 구성품으로 필요한 위치 …Source: 9step.tistory.com
Date Published: 11/18/2021
View: 556
반도체 후공정 – 테스트(Test)공정
반도체 후공정에서 이뤄지는 테스트(Test)란, 전기적 특성 검사를 통해 웨이퍼나 칩의 불량이 다음 공정으로 넘어가지 않도록 방지함으로써 손실을 …
Source: yooyouhea.tistory.com
Date Published: 3/18/2021
View: 3786
Package Test – 네이버 블로그
‘TEST’하면 보통 ‘시험’이라는 의미로 생각하기 쉬운데, 반도체 제조공정에서 TEST란 『검사』의 개념이 강합니다.
Source: m.blog.naver.com
Date Published: 12/17/2022
View: 644
주제와 관련된 이미지 반도체 테스트 공정
주제와 관련된 더 많은 사진을 참조하십시오 반도체 테스트 공정, 6분만에 이해시켜드립니다!!. 댓글에서 더 많은 관련 이미지를 보거나 필요한 경우 더 많은 관련 기사를 볼 수 있습니다.
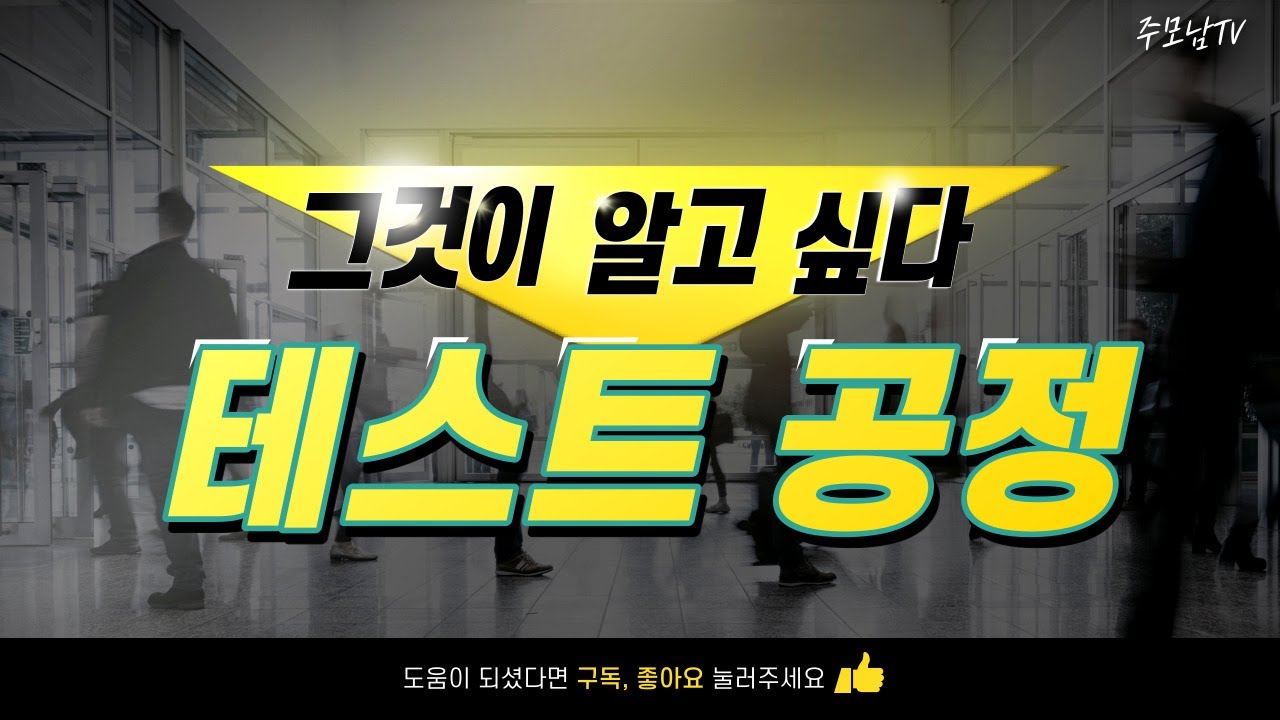
주제에 대한 기사 평가 반도체 테스트 공정
- Author: 주모남TV
- Views: 조회수 6,557회
- Likes: 좋아요 107개
- Date Published: 2021. 6. 5.
- Video Url link: https://www.youtube.com/watch?v=_0K8HzsBPp8
[반도체 특강] 테스트(Test), 반도체의 멀티 플레이어
반도체 후공정에서 이뤄지는 테스트(Test)란, 전기적 특성(Electrical Characteristics) 검사를 통해 칩(Chip)의 불량이 다음 공정으로 넘어가지 않도록 방지함으로써 손실을 최소화하는 과정입니다. 초창기의 테스트는 양산 제품에 대해 불량(영구적 오류)을 걸러내는 필터링 위주로 진행했습니다. 하지만 현재는 신뢰성 불량을 사전 차단하고, 수율을 향상시켜 원가 절감에 기여하며, 제품의 연구∙개발에 도움을 주는 등 그 역할이 점차 확대되고 있지요. 이번 장에서는 반도체의 멀티 플레이어, 테스트 공정에 대해 자세히 살펴보도록 하겠습니다.
1. 반도체 테스트 공정 Flow
<그림1> 반도체 테스트 공정 흐름도
수많은 공정을 거쳐 제작된 반도체는 각 공정이 제대로 수행됐는지 검증하기 위해 상온(섭씨 25도)에서 테스트를 진행합니다. 테스트는 크게 Wafer Test, Package Test, Module Test로 이뤄집니다.
고온과 저온에서 실시하는 신뢰성의 일종인 Burn-in/Temp Cycling 공정의 경우, 초창기에는 Package Test 공정에서만 실시했는데요, 점차 Wafer Test 공정의 중요성이 높아짐에 따라 Package Burn-in 항목이 다수 WBI(Wafer Burn-in)으로 옮겨졌습니다. 또한, 테스트와 Burn-in을 결합한 TDBI(Test During Burn-in) 개념으로 Burn-in을 진행함에 따라, 정식 테스트를 Burn-in 전후에 실시하는 복합형도 많이 활용되는 추세입니다. 이렇게 되면 공정 시간과 비용을 절약할 수 있게 되겠지요. Module Test에서는 PCB(Printed Circuit Board)와 칩의 연관 관계를 점검하기 위해 상온에서 DC(Direct Current, 직류 전류/전압) / Function(기능) 테스트를 진행한 뒤, Burn-in 대신 실제 고객 환경에서 칩을 동작해보는 실장 테스트를 진행하지요.
2. 반도체 테스트의 목적
<그림2> 반도체 테스트의 목적
반도체 테스트의 목적은 불량 칩을 골라내고, 앞서 진행했던 공정들을 점검해 개선하는 것입니다. 이 과정에서 다음 공정으로 불량 칩이 넘어가지 못하게 하는 선별률(Screenability)은 항상 중요한 이슈입니다. 따라서 Wafer Test는 불량 칩이 불필요하게 패키징(Packaging)되는 것을 방지해 원가를 절감하고, 나아가 수익성을 향상시키는 것이 목표이지요. Package Test는 불량 제품이 출하되는 것을 막아 고품질의 반도체를 고객에게 납품하기 위함입니다. 또한, 양품이 고객에게 전달된 이후에도 칩에 동작 오류(Fault)가 발생할 수 있는데, 유저가 일정 기간 칩을 오류 없이 안전하게 사용할 수 있도록 제조 과정에서 약한 칩을 미리 골라내어(제품의 전체 생존 기간 중 초창기/중기 불량을 선별) 신뢰성(Reliability)을 확보하는 것이 매우 중요합니다. 이렇게 진행된 테스트 결과(Performance)는 내부적인 피드백을 통해 공정을 개선하거나, 반도체 기술 및 제품의 연구∙개발에도 적극 활용되고 있습니다.
3. 반도체 테스트(공정 측면): Wafer Test / Package Test / Module Test
<그림3> 반도체 테스트의 종류 @양산단계
반도체 테스트는 공정 Step 관점에서는 Wafer Test, Package Test, Module Test로 구분할 수 있으며, 기능별로 구분할 경우 DC(Direct Current)/AC(Alternating Current)/Function/실장/신뢰성 테스트 등으로 나눌 수 있습니다.
Wafer Test에는 Fab 공정에서 만들어진 집적된 반도체 회로의 동작 여부를 검증하는 기초적인 테스트 항목들이 많이 포함돼 있습니다. 매우 가느다란 바늘을 칩의 패드에 밀착(Probing)해 전기적인 신호를 인가한 후, 회로를 거쳐 나온 결과인 전기적 특성을 비교∙측정해 최종적으로 판정(Die Sorting)하지요. 여기서 나온 불량 Tr(Transistor)은 우회하거나 양품 Tr로 대체하는데, 이는 레이저빔(Laser Beam)을 이용해 수선(Repair)하여 양품 칩으로 만들어 내는 방식입니다.
Package Test에는 신뢰성 테스트도 포함돼 있지만, 제품을 출하하기 전 최종적으로 전기적인 특성을 검사한다고 하여 파이널 테스트(Final Test)라고 부릅니다. Package Test는 가장 중요한 테스트 공정으로써 모든 테스트 항목이 집중돼 있는데요, 먼저 DC/AC 테스트와 Function 테스트에서 양품(Go)/불량품(No-Go)을 판정한 뒤, 양품들 중 속도별로 그룹을 가르는 Speed Sorting(ex. DRAM)을 진행해 고객이 요구하는 속도를 만족하는 제품을 확보합니다.
마지막으로 Module Test는 PCB에 8~16개의 칩을 탑재한 후 진행한다고 하여 보드 테스트(Board Test)라고도 합니다. Module Test에서는 DC/Function 테스트 후 실장 테스트를 진행, 되도록 고객이 실제 제품을 사용하는 환경에서 칩을 선별할 수 있도록 합니다. 이 과정에서 불량 칩이 발견되면 양품 칩으로 교환해 새롭게 모듈을 구성할 수 있지요.
4. 반도체 테스트(기능 측면): DC Test / AC Test / Function Test
4-1. DC Test
<그림4> DC Test 결과에 대한 판정 및 후속 조치
DC Test(혹은 DC Parametric Test)에서는 개별 Tr의 전기적 특성을 측정하는 EPM(Electrical Parameter Measurement)을 진행해 칩 내 개별 Tr들이 제대로 동작하는지 확인합니다. 구체적으로는 구조물들이 Open 혹은 Short 되었는지, 단자 간 누설전류들이 발생하는지, 여러 가지 종류의 입력/출력 전압들이 Spec 한계 내 있는지 등을 기본적으로 점검하지요.
예를 들어, 와이어(Wire)나 볼(Ball)이 들뜨거나 유실되었는지, 회로의 선이 서로 붙었는지 등 형태적인 불량 여부는 물론이고, 확산과 이온 주입 시의 농도 및 사용 가스의 종류 등 Fab과 Package 공정상의 치명적인 오류까지 전기적으로 검사하고 밝혀낼 수 있어야 합니다. 물론 100% 확인해 내기는 힘들겠지만요.
즉, DC Test는 Tr을 형성하기 위해 수행된 공정상의 매개변수(Process Parameter)가 제대로 진행되었는지를 검토한 결과(Performance)라고 볼 수 있습니다. 따라서 DC 테스트 결과들은 Limit 값(한계치)이 있어 최대치 혹은 최소치가 규정되어 있지요. 전(前)공정을 진행한 각 과정이 Spec-in으로 들어왔는지 여부를 측정한 결과와 미리 설정한 기준 모델을 비교해 차이가 있는지 확인하는 절차라고 볼 수 있습니다.
양산 단계에서 칩이 Spec-Out인 경우, 해당 칩은 Fail로 처리해 다이 본딩(Die Bonding) 시 배제합니다. 그러나 개발 단계일 때는 해당 사항을 피드백(Feedback)해 공정/제품/Technology에 대한 개선 조치를 취합니다(개발 단계에서는 Good Chip이든 Bad Chip이든 상관없이 사용된 Trial Wafer 자체를 Scrap시킴). 또한, 웨이퍼 측정 시 양산 단계일 때는 수율 때문에 TEG(Test Elements Group) 다이 대신 Scribe Line 내 TEG 영역을 만들어 테스트용 패턴(Pattern)으로 Tr/Diode/Capacitance/저항 등을 깔고 해당 부위를 측정합니다.
4-2. Function Test / AC Test
<그림6> 반도체 Electrical Test: DC, AC, Function Test
Function Test에서는 칩의 패드에 여러 종류의 테스트용 패턴(혹은 Vector Data)을 인가해 제공된 Truth Table과 일치되는 결과를 도출하는지를 점검합니다. 이는 단일 소자가 아닌 여러 소자(Column/Row 혹은 Block)를 한꺼번에 점검함으로써 간섭 현상이나 누설전류 등으로 인해 주변 Tr에 어떠한 영향을 끼치는지 등을 확인합니다. 이러한 Function Test에서는 각 제품마다 조건에 맞는 테스트용 패턴을 사용하는데요, 이때 패턴은 ‘0’과 ‘1’을 이용해 다양하게 만들어 셀(Cell)에 쓰기/읽기를 반복합니다.
AC Test는 시간 변수에 따른 입력이 주어졌을 때 Signal의 Set-up Time, Hold Time 등 Time 관련 사항을 주로 점검하고 제품의 동작 시간을 측정합니다. 이를 통해 DRAM 단품 같은 경우, 속도별로 담아 놓는 통(Bin)을 마련해 분리해내는 Bin-Sorting을 하지요.
5. 전기적 파라미터와 공정 변수의 연동
전기적 파라미터(Parameter) 중 가장 중요한 변수는 드레인 전류입니다(그 다음이 문턱전압, 스위칭 타임 순으로 볼 수 있습니다). 예를 들어 드레인 전류와 공정 변수의 연관 관계를 살펴보면, Technology가 고도화(ex. 12nm→7nm)된다는 것은 선폭이 미세화(이는 곧 게이트의 길이/폭과 채널의 길이/폭이 축소되는 형태적 변형의 의미)되고, 그에 따라 소스 단자에서 드레인 단자 사이를 지나가는 전자들의 통로인 채널 단면적을 좁게 형성(길이에 비해 단면적 영향이 더 큼)시켜야 한다는 것을 의미합니다. 이렇게 공정변수가 축소되면 드레인 전류(Id)가 줄어들게 되므로 선폭에 맞춰 드레인 전류의 스펙 한계값(Spec Limit)을 축소하여 재설정해야 하지요. 이와 같이 공정 변수에 맞추어 전기적 파라미터 값을 조정하거나 반대로 값을 줄일 수 없는 일정한 전류값을 유지해야 할 상황이라면 공정변수인 농도변수를 조정하는데, 소스/드레인 단자 형성 시 이온 주입 공정의 양이온 도즈량을 높여야 합니다. 드레인 전류와 마찬가지로 전압에 따른 커패시턴스(Capacitance)값이나 저항값 역시 DC/AC 측정값을 피드백 받아 공정변수를 재조정하거나 스펙의 한계값을 다시 설정합니다. 이렇듯 전기적 파라미터값은 공정 변수와 긴밀히 주고받는 관계로 연결돼 있습니다.
반도체 제품의 테스트는 종류가 매우 다양하며, 관점에 따라서도 여러 가지 방향으로 해석될 수 있습니다. 또한 공정 효율성을 높이고 원가를 낮추기 위해 패키지 레벨 테스트와 웨이퍼 레벨 테스트 항목을 교환하거나 섞기도 하며 그에 맞춰 공정을 변화시키지요. 이런 복합적인 요인들을 맞추기 위해 제품 설계에서 장비 및 공정 방법까지를 포함한 제품 개발 전략이 끊임없이 업데이트됩니다. 반도체 공정 전체와 Technology 및 고객에게 전반적으로 막대한 영향을 끼치는 과정이지요. 오늘 소개된 테스트의 공정 및 기능 측면 이외에도 육안 테스트 및 메카니컬 테스트 등이 있어 필요에 따라 불러내어 제품을 양품화 하는 데 제반 사항들을 최적화합니다.
※ 본 칼럼은 반도체/ICT에 관한 인사이트를 제공하는 외부 전문가 칼럼으로, SK하이닉스의 공식 입장과는 다를 수 있습니다.
반도체 TEST공정
728×90
SMALL
TEST 공정
#시작하며
반도체 후공정에서 이뤄지는 TEST란, 전기적 특성 검사를 통해 칩의 불량이 다음 공정으로 넘어가지 않도록 방지함으로써 손실을 최소화하는 과정이다. 현재 신뢰성 불량을 사전 차단하고, 수율을 향상시켜 원가 절감에 기여하며, 제품의 연구-개발에 도움을 주는 등, 그 역할이 점차 확대되고 있다.
수많은 제조공정을 거친 반도체 칩은, 마지막 절차인 TEST를 통해 불량품을 선별하게 된다. 반도체의 양품, 불량품 선별을 위해 반도체 제조과정에서는 다양한 TEST가 이루어지는데, 웨이퍼 단계에서 이루어지는 EDS(Elrctrical Die Sorting), 조립공정을 거친 패키지 상태에서 이루어지는 패키징공정(Packaging), 제품 출하 전 소비자의 관점에서 실시되는 품질테스트 등이 있다.
그 중에서, 먼저 첫번째 관문인 EDS공정은 웨이퍼 위에 전자회로를 그리는 FAB 공정(제조/생산)과 최종적인 제품의 형태를 갖추는 패키지 공정 사이에 진행된다. 즉 전기적 특성검사를 통해 개별 칩들이 원하는 품질 수준에 도달했는지 확인하는 공정이다.
#TEST 공정
TEST 공정 Flow
출처. SK hynix NEWROOM
수많은 공정을 거쳐 제작된 반도체는, 각 공정이 제대로 수행됐는지에 대한 검증을 위해 크게 Wafer Test, Package Test, Module Test의 테스트를 진행한다. 초창기 Package Test에서만 실시하던 Burn-in 공정의 경우, Wafer TEST공정의 중요성이 높아짐에 따라, 다수 항목이 Wafer Burn-in으로 옮겨졌다. 또한 TEST와 Burn-in을 결합한 TDBI(TEST During Burn-in) 개념으로 정식 테스트를 Burn-in 전후에 실시하는 복합형도 많이 사용하여 공정 시간과 비용을 절약하고 있다. Module TEST에서는 PCB(Printed Circuit Board)와 칩의 연관 간계 점검을 위해 상온에서 DC/Function 테스트를 진행한 뒤, 실제 고객 환경에서 칩을 동작해보는 실장 테스트를 진행한다.
반도체 테스트는 불량칩을 골라내고 앞서 진행한 공정을 점검/개선하는 것이다. 해당 과정에서 다음 공정으로 불량 칩이 넘어가지 못하게 하는 선별률(Screenbility)는 중요한 이슈이다.
* Wafer TEST – 불량 칩이 Packaging되는 것을 방지하여 수익성 향상
* Packaing TEST – 불량 제품이 출하되는 것을 막아 고품질 반도체 납품, 칩 오류 개선을 통한 신뢰성 확보
반도체 TEST 공정 분류
반도체 TEST 종류
반도체 TEST는 공정 Step 관점에서 위 그림과 같이 Wafer TEST, Package TEST, Module TEST로 구분할 수 있다.
* Wafer TEST
– 웨이퍼 상태에서 칩의 정상여부 검사
– 웨이퍼 검사장비에서 수행
* Package TEST
– 반도체 전/후 공정을 마친 후, 최종단계에서 Package의 정상적인 작동 유무를 평가
– Burn-in TEST 장비 사용
* Module TEST
– PCB에 반도체 소자가 여러개 장착되어 있는 Module사이에서 제대로 작동하는지를 검사
– Module 검사장비로 분류
#Wafer(EDS) TEST 공정
Wafer TEST 공정은, FAB과 Package공정의 중간, 즉 칩의 정상 여부를 검사하는 Probe Test 공정에 위치한다.
Wafer(EDS) TEST 공정과 수율
수율이 높은 것은, Wafer 한 장에서 나올 수 있는 정상적인 칩의 수가 많다는 뜻으로서, 설계된 최대 칩 수와 실제 생산된 정상적인 칩 수의 비율로서 정의된다. 수율이 높을수록 생산성이 높기 때문에, 반도체 생산라인에서는 수율을 향상시키는 일이 가장 중요하다.
수율향상 조건
출처. 한국기술교육대학교
Clean Room의 청정도 – 파티클, 온도, 습도의 조건을 잘 유지하는 것이 중요하다.
공정장비의 정확도 – 패턴을 형성하는 공정장비의 정확도
공정조건 – Clean Roon과 공정장비의 정확도가 만족된 경우에는, 공정 조건을 어떻게 설정할 것인지가 중요하다.
세부 공정
* ET TEST(Electrical Test) ⇒ 작동 여부 판별 기능
– 반도체 제조 공정 중 중요한 단위 공정
– 반도체 집적회로(IC) 동작에 필요한 개별 소자들에 대한 직류전압, 전류 등 전기적 특성의 파라미터 테스트
* Wafer Burn-in ⇒ 제품의 신뢰성 향상
– 제품 초기에 발생하는 높은 불량률 제거를 목적으로 한다.
– 웨이퍼에 일정 온도의 열을 가한 후, AC/DC 전압을 가해 제품의 취약, 결함 부분과 같은 잠재적인 불량요인을 발견.
* Pre Laser(Hot & Cold)
– 전기적 신호를 통해 웨이퍼 상의 칩들의 정상여부 판별
– Repair 가능한 칩은 수선공정에서 처리
– 특정 온도에서 발생하는 불량을 위해 상온보다 높거나 낮은 온도에서 진행
* Laser Repair & Post Laser
– 전 공정(Pre Laser)에서 불량이 발생하였지만 Repair가 가능한 칩을 모아 Laser Beam을 통해 수선하는 공정
– Wafer TEST 가운데 중요한 공정이다.
– 수선이 끝난 후 Post Laser 공정을 통해 수선 여부를 재차 검증
#마치며
오늘은 반도체 후공정인 TEST 공정에 대해 공부하였다. 후공정의 기술력은, 생산업체간의 경쟁력과 직결되는 문제로 부상함에 따라 그에대한 중요성은 계속해서 증가하고 있다. 다음 포스팅에서는, 패키징 공정에 대해 알아볼 것이다.
728×90
[반도체 공정] 반도체? 이 정도는 알고 가야지:(8) Wafer test & Packaging 공정
[반도체 공정] 반도체? 이 정도는 알고 가야지:(8)Wafer test & Packaging 공정
SK하이닉스 취준생이라면 꼭 알아야하는 반도체 공정! 7번째 공정 포스팅에 이어, 마지막 공정 관련 포스팅을 준비했습니다. 함께 알아볼까요?
SK Careers Editor 한수정
여러분 다들 한 번쯤은 남자친구 혹은 여자친구에게 줄 편지와 선물 준비해보신 적 있으시죠? (잠시 눈물을 닦아봅시다..) 반도체를 완성하기 위한 마지막 두 공정이 이와 매우 비슷한데요.
선물을 주기 전에 정성스레 쓴 편지에 오탈자는 없는지, 빠진 선물은 없는지, 케이크의 상태는 양호한지 최종적으로 체크하는 단계 ☞ 반도체 공정에서는 “Wafer TEST공정”
포장은 선물의 완성! 선물을 주기 전 꼼꼼한 포장하는 단계 ☞ 반도체 공정에서는 “Packaging”
# Wafer TEST공정이란?
Wafer TEST공정은 웨이퍼 상태에서 여러가지의 검사를 통해 각 칩들의 상태를 확인하는 과정을 말합니다. 지난 컨텐츠에서 살펴 본 공정과 최종적인 제품의 형태를 갖추는 패키징 공정 사이에 진행되는데요. 이 과정을 통해 웨이퍼 상태의 반도체 칩의 불량여부를 선별할 수 있고, 설계 상의 문제점이나 제조 상의 문제점을 발견해 수정할 수 있습니다. Wafer TEST공정을 거치면 이후 진행되는 패키징 공정 작업의 효율이 높아집니다.
# Wafer TEST공정의 네 단계
Wafer TEST공정은 반도체의 수율을 높이기 위해 반드시 필요한 공정입니다. 수율은 쉽게 말해 웨이퍼 한 장에서 사용할 수 있는 정상적인 칩 수를 계산한 것인데요. 수율이 높을수록 생산성이 높다는 의미가 됩니다. 그러므로 높은 수율을 얻는 것은 매우 중요합니다. 그렇다면 Wafer TEST공정은 크게 어떻게 이루어져 있을까요?
1) EPM & WFBI
EPM은 Electrical Parameter Monitoring의 약자로 반도체 직접회로(IC) 동작에 필요한 개별소자들의 전기적 직류 전압, 전류 특성의 파라미터를 테스트해 잘 작동하는지를 판별하는 과정입니다. WFBI는 Wafer Burn In의 약자로 웨이퍼에 일정 온도의 열을 가한 다음 AC/DC 전압을 가해 잠재적 불량 요인을 찾아내는 과정입니다. 이 두 과정을 통해 제품 초기에 발생하는 높은 불량률을 효과적으로 제거할 수 있습니다.
2) Hot & Cold Test
전기적 신호를 통해 웨이퍼 상의 각 칩들에 이상이 있는지 판정합니다. 이상이 있는 칩 중 수선이 가능한 것들은 수선 공정에서 처리할 수 있도록 정보를 저장하는데요. 이 때, 특정 온도에서 발생하는 불량을 판별하기 위해 높은 온도 혹은 낮은 온도에서 테스트합니다.
3) Repair & Final Test
불량품에 대해서는 Electrical Rupture를 통해 Repair하고, 수선이 끝나면 Final Test를 통해 수선이 제대로 이루어졌는지 검증하고 양품인지 불량품인지를 최종적으로 판단합니다.
4) Inking
말 그대로 ‘잉크를 찍는 공정’입니다. 불량 칩에 특수 잉크를 찍어 육안으로 불량칩을 식별할 수 있도록 하는 과정인데, 과거에는 실제 잉크를 찍었지만 현재는 실제 잉크를 찍지 않고 전산화하여 관리하고 있습니다. 불량으로 전산 처리된 칩은 조립 작업이 진행되지 않으므로 시간이나 경제적 측면에서 긍정적인 효과가 있겠죠? Inking공정까지 마친 웨이퍼는 품질 검사를 거쳐 조립 공정으로 이동됩니다.
# Packaging공정이란?
Packaging공정을 더 세부적으로 나누면, Package공정과 Package Test공정으로 나눌 수 있습니다.반도체 칩은 전자기기의 구성품으로서 필요한 위치에 장착되어야 하기 때문에 적절한 모양으로 패키징되어야 하는데요. 외부의 전원 공급 및 입출력 신호 전류들이 흐를 수 있도록 만들어주어야 하고, 반도체 칩을 외부로부터 보호할 수 있어야 합니다.
# Package공정의 여덟 단계
둥근 웨이퍼가 작은 반도체칩이 되기까지 다양한 과정을 거치게 되는데요. Package공정의 각 과정에 대해 조금 더 알아볼까요?
1) Back Grind
FAB작업이 완료된 두꺼운 웨이퍼를 얇은 다이아몬드 휠로 연마해 얇은 반도체가 될 수 있도록 만드는 과정입니다.
2) Wafer Saw
다수의 칩으로 되어있는 웨이퍼를 낱개의 칩으로 분리합니다.
3) Die Attach
분리한 칩 중에서 양품으로 선별된 개별 칩을 웨이퍼 상에서 떼어내어 외부와 전기적 연결 단자인 Substrate 기판에 접착합니다.
4) Wire Bond
칩의 단자와 Substrate의 단자를 전기적으로 연결해줍니다.
5) Mold
습기, 열, 물리적 충격 등으로부터 보호하기 위해 열경화성 수지인 EMC로 기판을 감싸줍니다.
6) Marking
레이저를 이용해 제품번호를 각인합니다.
7) Solder Ball Mount
PCB와 Package를 전기적으로 연결할 수 있도록 Substrate에 Solder ball을 부착해 아웃단자를 만들어 주는 과정입니다.
8) Saw Singulation
Substrate를 한 개의 개별 제품으로 분리해주는 과정으로, Package의 마지막 단계입니다.
#Package Test의 세 단계
이렇게 완성된 반도체는 최종적으로 Package Test를 거쳐야 하는데요. DRAM의 패키지 테스트 과정을 예시로 살펴볼까요?
1) DC Test & Burn-in
DC Test는 설계 및 조립공정을 거치면서 발생된 불량을 선별하는 공정이며, Burn-in공정은 극한 조건을 가한 후 테스트를 진행함으로써 불량 가능성이 있는 제품을 사전에 검사하는 것입니다. 이 과정을 통과해야 반도체 칩이 들어가는 전자기기가 오류 없이 작동할 수 있는 신뢰성을 갖게 됩니다.
2) Main Test
DC Test Burn in 을 통과한 제품들은 상온, 저온 공간에서 전기적 특성과 기능을 검사 받습니다. 특히 Main test에서는 반도체분야 국제표준인 JEDEC Spec을 맞추기 위한 까다로운 검사가 진행될 뿐만 아니라, 추가로 고객이 요구한 다양한 환경에 맞추어 테스트를 진행합니다. 이 테스트를 통과해야만 Final Test로 가게 됩니다.
3) Final Test
고온에서 반도체의 전기적 특성과 기능을 검사 받는 과정으로 ‘완벽한 반도체’가 되기 위한 마지막 단계입니다.
이번 포스팅을 마지막으로, 지금까지 반도체 공정에 대해 쭉 살펴보았는데요. 면접에서 반도체 공정 관련 질문이 들어온다면 자신 있게 대답하실 수 있었으면 좋겠습니다. SK Careers Journal에서 준비한 반도체 공정 포스트로 SK하이닉스에 더욱더 가까워지는 여러분이 되시길 바랄게요!
반도체 패키지 테스트 공정 관련 국내 기업
패키지 테스트 공정은 반도체 완제품 완성 후, 출하전에 불량여부를 선별하기 위해 최종적으로 진행하는 테스트 공정입니다. 반도체를 테스트 장비(Tester)에 넣고 다양한 조건의 전압, 전기신호, 온도, 습도 등을 가하면서, 반도체가 해당 조건별로 어떤 전기적 특성, 기능적 특성, 동작 속도 등을 보이는 지를 측정합니다. 이 결과를 분석해 양품(Go)과 불량품(No-Go)을 판정하게 되고, 결과를 제조공정과 조립공정에 피드백함으로써 품질 개선에도 기여하게 됩니다. 패키지 테스트에는 다음과 같은 기능 테스트들이 포함됩니다.
구분 설명 DC Test
(DC Parametric Test) 개별 Tr(Transistor)에 전기적 특성을 측정하는 EPM(Electrical Parameter Measurement)를 진행해 칩내 개별 Tr들이 제대로 동작하는 지 여부를 검사합니다.
– 구조물들의 Open 혹은 Short 여부
– 단자 간 누설전류 발생 여부
– 여러 종류의 입력/출력 전압들이 허용 벙위 내인지 여부 Function Test 단일 소자가 아닌 여러 소자(Column/Row, Block)에 대해 다양한 종류의 테스트용 전기신호 패턴(Vector Data)를 주입해 소자들간 간섭현상이나 누설전류 등의 오류 없이 제대로 동작하는 지 여부를 검사합니다. AC Test 시간변수에 따른 입력이 주어졌을 때 Signal의 Set-up Time, Hold Time 등의 Timing 관련 사항을 주로 점검합니다. 이를 통해 제품의 동작시간을 측정하고, 제품을 동작시간별로 분류합니다.
패키지 테스트 공정 장비 관련 기업
다음은 반도체 패키지 테스트 공정에 사용하는 장비 관련 사업을 하고 있는 국내 기업들입니다.
기업명 관련 제품 기업 개요 디아이 – 패키지 번인 테스터 장비 – 반도체 검사장비 부문은 1955년 과학기기 수입 판매업으로 출범하여 반도체 검사장비 등 초정밀 시험장비의 제조 및 수입업을 영위하고 있음.
– 주요 사업은 반도체 검사장비 사업부문, 전자파 차폐체(EMC) 등을 제조하는 전자부품 사업부문, 수(水)처리 관련 환경사업, 음향·영상기기 사업부문으로 구성됨.
– 2021년 3월말 현재 연결대상 종속회사로는 디지털프론티어, 두성산업, 디아이엔바이로 등 국내외에 총 8개사임. 미래산업 – Memory Test Handler, Burn-in Sorter, Logic Test Handler, Module Test Handler -동사는 1983년 1월 27일 설립하였고, 1996년 11월 22일자로 주식을 한국거래소에 상장함.
– Test Handler 등 반도체 장비가 주요재화인 ATE사업부와 Chip Mounter, 이형부품삽입기 등이 주요재화인 SMT사업부로 구분됨.
– 반도체 검사장비(Test Handler)는 반도체 시장의 주기적인 경기순환 및 정보기술(IT) 산업의 경기 변동 상황에 밀접하게 연관되어 있음. 성우테크론 – 2D/3D 자동외관검사 장비 – 동사는 1997년 4월 설립되어 반도체 검사장비의 제조 및 반도체 부품 제조를 주업으로 하고 있고 2001년 12월 코스닥시장에 상장함.
– 동사 주요사업의 내용은 부품사업부문, PCB사업부문, 장비사업부문으로 구성되어 있음.
– 동사의 종속회사에 포함된 회사가 영위하는 사업은 반도체 구성재료인 IC, TR제품 등의 리드프레임 제조업, 전기전자 부품제조 및 조립업, 반도체 관련제조 설비업, 부동산임대업이 있음. 인텍플러스 – 2D/3D 반도체 패키지 자동외관검사 장비 – 벤처기업 육성에 관한 특별법에 의해 인증받은 벤처기업.
– 동사는 머신비전기술을 통해 표면 형상에 대한 영상 데이터를 획득, 분석 및 처리하는 3D/2D 자동외관검사장비 및 모듈을 개발하여 판매하고 있음.
– 동사는 SSD 외관검사장비 분야의 1사업부, 플립칩 반도체의 서브스트레이트, WLP/PLP 검사장비 분야의 2사업부, OLED 및 LCD 검사 분야의 3사업부, 2차전지 및 자동차 분야의 4사업부로 나뉘어 있음 탑엔지니어링 – Semiconductor Parameter Analyzer – 동사는 반도체, LCD, LED 및 OLED 및 카메라모듈 공정장비를 개발, 제조 및 판매를 주된 사업으로 하고 있음.
– 국내에 공정장비 제조공장, 및 R&D센터를 보유하고 있으며, 중국 및 대만에 현지 사무소를 운영중에 있음. 또한 계열회사를 통해 부품과 신소재 관련 제품으로 사업영역을 확장하고 있음.
– LCD 장비인 디스펜서는 약 60%의 높은 점유율로 1위를 차지하고 있음. 유니테스트 – Memory Tester
– Storage Tester – 동사는 반도체 후공정(반도체 검사 장비)업체로서 메모리 모듈 테스터 및 메모리 컴포넌트 테스터를 국내 업계 최초로 개발 완료하여 반도체 장비의 국산화를 주도하고 있음.
– 동사는 기존의 SI 태양전지를 대체할 수 있는 보다 저렴하면서 고효율을 낼 수 있는 페로브스카이트 물질을 이용한 신규의 태양전지를 개발중임.
– 주요 매출 구성은 태양광 사업 60.1%, 반도체 검사장비 39.9% 등으로 이루어짐. 테크윙 – Memory/Logic/Module Test Handler – 동사는 반도체 후공정 라인에서 사용되는 자동화 장비를 설계, 개발, 판매중이며, 주력 제품은 양품과 불량품을 자동으로 분류하는 반도체 테스트 핸들러가 있음.
– 연결대상 종속회사로는 디스플레이 패널, 모듈 공정용 전기, 광확검사 장비 제조업체 ‘이엔씨테크놀러지’ 포함 6개사가 있음.
– 2021년 3월 기준 매출구성은 반도체 검사장비(테스트 핸들러, C.O.K 등)가 87.47%로 가장 큰 비중을 차지하고 있음. 제이티 – Test Handler
– Burn-in Sorter
– 2D/3D 자동외관검사 장비 – 동사는 1998년 설립되어, 반도체 검사장비 관련 사업 개발 및 판매를 주요 사업으로 영위함.
– 당사는 설계 및 개발 전문 기업으로 생산설비는 보유하지 않고 외주 생산함. 반도체 검사장비 시설은 천안에서, 산업용 특수가스 및 가스설비시설은 진천에서 생산 중임.
– 주력사업인 번인소터(Burn-in Sorter)는 메모리 반도체 산업 성장에 따라 안정적인 주 수익원 역할을 꾸준히 수행하고 있음. 엑시콘 – DRAM & Nand Burn-in Tester
– Memory Component& Module Tester
– Storage Tester – 동사는 2001년 설립되어 반도체 메모리 Component, Module 제품 등의 테스트를 위한 시스템의 개발, 제조 및 판매 사업을 영위함.
– 반도체 성능 및 신뢰성 검사하는 반도체 장비 사업과 불량 원인 분석 등을 통해 설계 및 제조 공정상 수율을 개선하는 테스트 사업을 영위중.
– 자체 개발된 장비를 기반으로 외부 반도체 제조업체들을 대상으로 한 반도체 Test Service Biz를 운영하고 있음. 고영 – 3D 자동외관검사 장비 – 동사는 전자제품 생산용, 반도체 생산용 3D 납도포검사기, 3D 부품 장착 및 납땜 검사기, 반도체 Substrate Bump 검사기 등을 제조해 판매하는 것을 주요 사업으로 영위함.
– 전자 제조 전문 서비스(EMS)업체,휴대폰, 자동차 부품 제조업체 등에 제품을 공급함.
– Japan Koh Young Co.,Ltd, Koh Young Europe Gmbh 등 5개 회사를 연결대상 종속회사로 보유함. 예스티 – MBT Tester
– Chamber – 동사는 2000년 3월 주식회사 영인테크로 설립되어, 2006년 1월 상호를 예스티로 변경하였으며, 반도체 및 디스플레이 장비, 반도체 부품을 제조하는 기업임.
– 반도체용 열처리 장비를 개발을 시작으로 고온용 열처리 장비 개발을 완료 및 2010년 삼성디스플레이에 장비 공급을 시작으로 디스플레이 사업에 진출함.
– 주요 매출 비중은 환경안전 34.69%, 반도체장비 31.88%, 디스플레이장비 16.06% 로 구성됨. 제너셈 – Test Handler
– Vision Inspection – 동사는 반도체 제조 후공정에 적용되는 pick & place, inspection, test handler 등 다양한 반도체 후공정 검사 및 이송장비를 설계, 제조하는 장비 전문 기업임.
– 반도체 후공정 자동화 장비의 주력 상품으로Laser Marking, Test Handler, Inspection, Pick & Place외 Automation 장비 등이 있음.
– 반도체 후공정 장비가 주요 매출(100%)을 구성하고 있음. 네오셈 – DRAM/NAND Burn-In Tester, Memory Module Tester
– SSD Tester(세계 점유율 1위)[장비]
– Test Automation – 동사는 2002년 설립되어 대신증권 제3호 기업인수목적주식회사와 합병을 통해 2019년 코스닥 시장에 상장하였음.
– 동사는 반도체 검사장비 전문 기업으로 주사업은 SSD 검사장비와 MBT로 구성되어 있음. 특히 글로벌 SSD 검사장비 M/S 1위 기업으로 글로벌 SSD 상위 제조사에 모두 장비를 공급하고 있음.
– 현재 주력제품은 4세대 SSD 검사장비이며, 5세대 SSD 검사장비의 기반기술을 이미 확보한 기술 선도 기업임. 자비스 – PCB, SMT, 반도체 X-ray 검사장비 – 동사는 2002년 4월 6일에 설립되었으며, 2015년 11월 17일 한국거래소 코넥스시장에 주식을 상장하였으며, 2019년 11월 15일 코스닥시장으로 이전 상장함.
– 동사는 코스닥 상장을 위해 2019년 05월 07일에 아이비케이에스제5호기업인수목적(주)와 합병계약을 체결하였으며, 2019년 11월 01일(합병등기일)에 합병을 완료함.
– 동사는 산업용부품검사장비와 식품이물검사장비 제조업을 주요 사업으로 영위하고 있음.
패키지 테스트 공정 부품 관련 기업
다음은 반도체 패키지 테스트 공정에 사용하는 부품 관련 사업을 하고 있는 국내 기업들입니다.
기업명 관련 제품 기업 개요 오킨스전자 – Burn-in Socket
– Test Socket
– Module Socket – 동사는 1998년 4월 반도체 검사용 소켓 등의 제조 및 판매를 주사업목적으로 설립되었으며, 2014년 12월 코스닥시장에서 상장함.
– 동사와 종속회사는 반도체 검사용 소켓 제조 사업과 반도체 테스트 용역 사업을 영위함. 종속회사로는 한국영다반도체, Vision Tech (Suzhou) 등 국내외에 2개사가 있음.
– 반도체 Chip제조 장비에 장착되어 소모성 원부자재로 사용되는 Magnetic Collet 제조사업을 시작함. ISC – 반도체테스트용 실리콘러버소켓(Silicone Rubber Contactor: iSC) 등
– 세계 시장점유율 1위 – 동사는 2001년 2월 반도체 및 전자 부품 검사장비의 핵심 부품인 후(後)공정 테스트 소켓 제품 생산 등을 목적으로 설립되었으며 메모리, 시스템반도체테스트 소켓 제품을 공급중.
– 종속회사로는 ISC International INC, ISC VINA MANUFACTURING, ISC Japan R&D Center, SMATECH INC, ISCM, ITMTC가 있음.
– 반도체 테스트 소켓 분야에서 세계 1위의 시장점유율을 차지함. 마이크로컨텍솔 – Burn-in Test Socket
– Module Test Socket – 동사는 반도체 검사용 소모품인 IC소켓(IC Socket)을 위주로 한 각종 반도체 및 통신기기 접촉부품을 생산 운용 및 써멀프로덱터 가전 사업을 운용하고 있음.
– 아이씨소켓은 대규모 자본 지출을 수반하는 설비투자 성격보다 반도체 제조 수량에 직접 연관된 소모성 특성에 따라 반도체 생산공정 내 경기변동성이 상대적으로 낮음.
– 매출비중은 B/I소켓 65.26%, Module소켓 16.09% 등으로 구성됨. 마이크로프랜드 – Test Socket
– Test Interposer – 주요 제품인 프로브 카드는 웨이퍼 테스트(Wafer Test)에 소요되는 고부가가치의 소모성 부품으로 경쟁력이 있음.
– 독자적인 MEMS 공정기술을 개발하여 12인치 세라믹 기판을 적용한 MEMS 공정 기술을 확보하고 있음.
– 현재 개발하고 있는 기술은 극 초소형화 기술이므로 현재 수십 Micro 단위에 있는 피치에 충분히 대응할 수 있어 향후 시장 경쟁력 유지 가능. 타이거일렉 – Load Board PCB
– Socket Board PCB
– Burn In Board – 동사는 2000년 7월 설립되어, Rigid PCB 반도체 제조공정 중 후 공정인 검사공정에서 사용되는 PCB를 주로 생산.
– 경쟁사 대비 특허받은 반자동 리벳용 크램핑 장치를 사용함으로써 양품 회수율을 극대화시키는 경쟁력 있음.
– 매출구성은 PROBE CARD 51.78%, LOAD BOARD 16.21%, 일반 BOARD 21.53%, SOCKET BOARD 9.08% 등으로 이루어짐. 디아이 – 메모리 번인 보드 – 반도체 검사장비 부문은 1955년 과학기기 수입 판매업으로 출범하여 반도체 검사장비 등 초정밀 시험장비의 제조 및 수입업을 영위하고 있음.
– 주요 사업은 반도체 검사장비 사업부문, 전자파 차폐체(EMC) 등을 제조하는 전자부품 사업부문, 수(水)처리 관련 환경사업, 음향·영상기기 사업부문으로 구성됨.
– 2021년 3월말 현재 연결대상 종속회사로는 디지털프론티어, 두성산업, 디아이엔바이로 등 국내외에 총 8개사임. 리노공업 – Test Socket – 동사는 1978년 11월 리노공업사로 창업 이후 1996년 12월 법인전환을 하였으며, 2001년 코스닥시장에 주식을 상장함.
– 전량 수입에 의존하던 검사용 PROBE와 반도체 검사용 소켓을 자체브랜드로 개발하여 제조 및 판매하는 사업과 초음파 진단기 등에 적용되는 의료기기 부품을 제조 및 판매하는 사업 등을 영위하고 있음.
– 반도체 테스트 시장의 요구에 LEENO PIN과 IC TEST SOCKET 등으로 대응하고 있음. 테크윙 – COK
– Interface Board – 동사는 반도체 후공정 라인에서 사용되는 자동화 장비를 설계, 개발, 판매중이며, 주력 제품은 양품과 불량품을 자동으로 분류하는 반도체 테스트 핸들러가 있음.
– 연결대상 종속회사로는 디스플레이 패널, 모듈 공정용 전기, 광확검사 장비 제조업체 ‘이엔씨테크놀러지’ 포함 6개사가 있음.
– 2021년 3월 기준 매출구성은 반도체 검사장비(테스트 핸들러, C.O.K 등)가 87.47%로 가장 큰 비중을 차지하고 있음. 티에스이 – I/F Board
– Load Board
– Test Socket – 반도체 및 OLED 검사장비를 제조, 판매하는 회사로 반도체 및 OLED의 전기적/광학적 특성을 검사하기 위한 Total Test Solution을 제조 및 판매함.
– 웨이퍼 상태를 테스트하기 위한 프로브카드와 후공정 최종 단계에서 검사를 위한 인터페이스보드, 로드보드, 테스트 소켓 그리고 OLED 테스터와 자동화 설비가 있음.
– MEMS(초소형 정밀기계기술)기술력과 설비를 갖추어 핵심 미세부품등을 제조 및 개발하고 있음.
패키지 테스트 공정 용역 관련 기업
다음은 반도체 패키지 테스트 공정 관련 용역을 사업으로 하고 있는 국내 기업들입니다.
기업명 관련 제품 기업 개요 SFA반도체 – WLCSP용 Wafer Test, Final Test 용역 – 동사는 충남 천안시 서북구 백석공단7로 16에 위치하며 1998년 6월 30일에 설립되었고, 2001년 5월 2일 코스닥시장에 상장됨.
– 동사는 계열회사 중 두 회사는 코스닥 상장사임.
– 동사는 반도체 산업의 후공정 분야인 반도체 조립 및 TEST제품을 주력으로 생산하고 있으며, 삼성전자, Micron, SK하이닉스 등 세계 유수의 반도체 업체들에게 최첨단 반도체 패키징 솔루션을 제공하고 있음. 하나마이크론 – 반도체 테스트 용역 – 동사는 2001년 8월 23일에 설립되어 2005년 10월 11일에 주식을 코스닥시장에 상장함.
– 동사의 경영진은 재무제표를 승인하는 시점에 연결실체가 예측가능한 미래기간 동안 계속기업으로서 존속할 수 있는 충분한 자원을 보유한다는 합리적인 기대를 가지고 있음.
– 반도체 산업의 BACK-END 분야인 반도체 조립 및 TEST 제품을 주력으로 생산하고 있으며 업계선두의 반도체 패키징 기술을 보유하고 있음. 네패스아크 – 패키지 테스트 용역 – 동사는 네패스 반도체사업부 내 Test 사업부문이 물적분할하여 2019년 4월 1일 설립되었으며, 반도체 제조관련 테스트 및 엔지니어링 서비스, 반도체 시험 생산업, 반도체 제품 도소매업 등을 사업으로 영위함.
– 동사는 네패스를 모회사를 두고 외주 형태로 진행 되고 있으며, 삼성전자향 PMIC, DDI 등에 대한 Test 물량을 확보하여 성장하고 있음.
– 2020년 11월 17일 코스닥 시장에 신규상장함. 성우테크론 – L/F 및 PCB 패키지 검사 용역 – 동사는 1997년 4월 설립되어 반도체 검사장비의 제조 및 반도체 부품 제조를 주업으로 하고 있고 2001년 12월 코스닥시장에 상장함.
– 동사 주요사업의 내용은 부품사업부문, PCB사업부문, 장비사업부문으로 구성되어 있음.
– 동사의 종속회사에 포함된 회사가 영위하는 사업은 반도체 구성재료인 IC, TR제품 등의 리드프레임 제조업, 전기전자 부품제조 및 조립업, 반도체 관련제조 설비업, 부동산임대업이 있음. 오킨스전자 – Package Test 용역 – 동사는 1998년 4월 반도체 검사용 소켓 등의 제조 및 판매를 주사업목적으로 설립되었으며, 2014년 12월 코스닥시장에서 상장함.
– 동사와 종속회사는 반도체 검사용 소켓 제조 사업과 반도체 테스트 용역 사업을 영위함. 종속회사로는 한국영다반도체, Vision Tech (Suzhou) 등 국내외에 2개사가 있음.
– 반도체 Chip제조 장비에 장착되어 소모성 원부자재로 사용되는 Magnetic Collet 제조사업을 시작함. 엑시콘 – 패키지 테스트 용역 – 동사는 2001년 설립되어 반도체 메모리 Component, Module 제품 등의 테스트를 위한 시스템의 개발, 제조 및 판매 사업을 영위함.
– 반도체 성능 및 신뢰성 검사하는 반도체 장비 사업과 불량 원인 분석 등을 통해 설계 및 제조 공정상 수율을 개선하는 테스트 사업을 영위중.
– 자체 개발된 장비를 기반으로 외부 반도체 제조업체들을 대상으로 한 반도체 Test Service Biz를 운영하고 있음. 에이팩트 – 패키지 테스트 용역 – 동사는 2007년 6월 반도체 제조 관련 테스트 및 엔지니어링 서비스를 주요 사업 목적으로 설립되어 현재 반도체 후공정 중 테스트 외주 사업을 영위함.
– 사업 초장기에는 NAND Flash 위주 사업을 진행하였으나, 현재는 DRAM 테스트 사업을 위주로 진행 중임.
– 주요 사업은 DRAM, NAND Flash, MCP 등 메모리 테스트 및 EOL(End of Line) 공정임. 반도체테스트가 주요 매출(100%)을 구성하고 있음.
[반도체 8대 공정] 8탄, 완벽한 반도체로 태어나기 위한 첫 번째 테스트 ‘EDS공정’ – 삼성반도체이야기
수많은 제조공정을 거친 반도체 칩은 마지막 절차인 테스트를 통해 양품, 불량품을 선별하게 됩니다. 반도체 제조과정에서는 다양한 테스트가 이루어지는데요. ▲웨이퍼 완성 단계에서 이루어지는 EDS공정(Electrical Die Sorting), ▲조립공정을 거친 패키지 상태에서 이루어지는 패키징공정(Pakaging), 그리고 ▲제품이 출하되기 전 소비자의 관점에서 실시되는 품질 테스트 등이 있습니다.
이번 시간에는 완벽한 반도체로 태어나기 위한 첫번째 관문 EDS공정에 대해 알아보겠습니다.
반도체 수율 향상과 직결된 EDS공정
EDS공정(Electrical Die Sorting)은 웨이퍼 위에 전자회로를 그리는 FAB 공정과 최종적인 제품의 형태를 갖추는 패키지 공정 사이에 진행됩니다. 즉 전기적 특성검사를 통해 개별 칩들이 원하는 품질 수준에 도달했는지를 확인하는 공정으로써 그 목적은 아래와 같습니다.
웨이퍼 상태 반도체 칩의 양품/불량품 선별
불량 칩 중 수선 가능한 칩의 양품화
FAB 공정 또는 설계에서 발견된 문제점의 수정
불량 칩을 미리 선별해 이후 진행되는 패키징공정 및 테스트 작업의 효율 향상
먼저 전기적 특성검사를 통해 각각의 칩들이 원하는 품질 수준에 도달하는지 체크합니다. 그 후 양품 가능 여부를 판단해 수선(Repair) 가능한 칩은 다시 양품으로 만들고, 불가능한 칩은 특정 표시(Inking)를 통해 불량으로 판정합니다. 불량으로 판정된 칩은 이후 공정에서 제외되어 효율을 높일 수 있습니다.
EDS공정은 반도체의 수율을 높이기 위해 반드시 필요한 공정입니다. 수율은 웨이퍼 한 장에 설계된 최대 칩(Chip) 개수 대비 생산된 양품(Prime Good) 칩의 개수를 백분율로 계산한 것으로, 반도체의 생산성과 직결됩니다.
EDS공정은 프로브 카드(Probe Card)에 웨이퍼를 접촉시켜 진행됩니다. 프로브 카드에 있는 수많은 미세한 핀(Pin)이 웨이퍼와 접촉해 전기를 보내고 그 신호를 통해 불량 칩을 선별하게 됩니다.
EDS공정의 4단계
EDS공정은 세분화된 여러 단계가 있지만, 크게 4단계로 나눌 수 있습니다.
1단계 – ET Test & WBI(Electrical Test & Wafer Burn In)
ET Test(Electrical Test)는 반도체 집적회로(IC) 동작에 필요한 개별소자들(트랜지스터, 저항, 캐패시터, 다이오드)에 대해 전기적 직류전압, 전류특성의 파라미터를 테스트하여 동작 여부를 판별하는 과정입니다. 반도체 칩(Chip)으로 행하는 첫 테스트라고 볼 수 있습니다.
이어지는 WBI공정(Wafer Burn In)은 웨이퍼에 일정 온도의 열을 가한 다음 AC(교류)/DC(직류) 전압을 가해 제품의 결합, 약한 부분 등 잠재적인 불량 요인을 찾아냅니다. 제품의 신뢰성을 효과적으로 향상시키는 공정입니다.
2단계 – Hot/Cold Test
Hot/Cold 공정에서는 전기적 신호를 통해 웨이퍼 상의 각각의 칩 중 불량품이 있는지 판정합니다. 수선 가능한 칩은 수선 공정에서 처리하도록 정보를 저장하는데요. 이때, 특정 온도에서 정상적으로 동작하는지 판별하기 위해 상온보다 높고 낮은 온도의 테스트가 병행됩니다.
3단계 – Repair / Final Test
Repair 공정은 EDS공정에서 가장 중요한 단계인데요.
Repair공정에서는 Hot/Cold 공정에서 수선 가능으로 판정된 칩들을 수선하고, 수선이 끝나면 Final Test 공정을 통해 수선이 제대로 이루어졌는지 재차 검증하여 양/불량을 최종 판단합니다
4단계 – Inking
Inking 공정은 불량 칩에 특수 잉크를 찍어 육안으로도 불량을 식별할 수 있도록 만드는 공정을 의미합니다. Hot/Cold Test공정에서 불량으로 판정된 칩, Final Test공정에서 재검증 결과 불량으로 처리된 칩, 그리고 웨이퍼에서 완성되지 않은 반도체 칩(Dummy Die) 등을 구별하는데요. 과거의 Inking 공정은 불량 칩에 직접 잉크를 찍었으나 현재는 Data만으로 양/불량을 판별할 수 있도록 처리하고 있습니다. 이렇게 처리된 불량 칩은 조립 작업을 진행하지 않기 때문에 조립 및 검사 공정에서 사용되는 원부자재, 설비, 시간, 인원 등의 손실 절감 효과가 있습니다.
Inking공정을 마친 웨이퍼는 건조(Bake)된 후, QC(Quality Control) 검사를 거쳐 조립공정으로 옮겨지게 됩니다.
완벽한 반도체를 위한 여정이 이제 얼마 남지 않았는데요. 다음 시간에는 반도체 칩을 기기에 탑재하기 적합한 형태로 만드는 패키징(Pakaging) 공정에 대해 알아보겠습니다.
[반도체 공부] 후공정(test & package)
728×90
반응형
[반도체 후공정]Packaging(Assembly), Test 공정을 후 공정이라 한다. 반도체 칩, 즉 집적회로(IC)를 기판이나 전자기기의 구성품으로 필요한 위치에 장착하기 위해 그에 맞는 포장을 하는 것, 반도체 칩과 수동소자(저항, 콘덴서 등)로 이루어진 전자 하드웨어 시스템에 관련된 기술을 통칭
기기에서의 신호가 잘 통하도록 하는 신호연결, 전력이 일정하게 유지되도록 하는 전력 공급, 열 관리, 외부의 충격으로부터 보호하는 칩 내부 보호가 Key Factor이다.
후공정이 중요해지는 이유: 무어의 법칙이 깨졌고, 반도체 전공정 직접도의 개선한계가 나타나고 있다. 또한 28nm 이하 반도체 전공정 투자 비용이 증가 하고 있다. 후공정의 기술발달이 생산업체 간의 경쟁력 차이를 발생시킬 것이다.
미세공정의 제한: 10nm대에서부터 immersion ArF(불화아르곤)를 사용하는 기존의 노광 공정 기술+더블 패터닝 조합의 한계가 나타남에 따라 쿼드러플 패터닝이 필요하다. EUV장비의 경우 효율대비 비용 측면의 문제가 있고 , 미세화가 진행됨에 따라 이웃한 셀과의 간격이 좁아지면 서 상호 셀간의 전자가 누설되는 간섭현상 심화.
Turn Key Solution : Package와 Test를 한번에 하여 Chip을 받아 한 회사 안에서 모든 공정을 처리. TSV(Through silicon via), InFO등과 같은 후공정 기술들을 통해 높은 가치를 제공.
*TSV : 칩을 적층할 때 빛을 발하는 방법으로 칩들을 관통시킨 후 전도성 물질로 채워 칩간의 전기적 신호를 전달하는 방식. 빠른속도, 높은 밀도, 얇고 작은 크기를 가지고 있지만 안정적인 수율의 이슈가 있다.
Wafet test
EDS(electrical Die Sorting) : 반도체 패키지 공정의 첫 번째 공정으로, Wafer에 대한 검사와 평가를 하여 다음 과정으로 진행 여부를 결정하는 test 공정. Probe card 를 이용하여 Wafer die에 전도성 Tip을 접촉시켜 전기적 신호를 연결하여 DC test 진행.
Lamination
Lamination Tape: 크랙, warpage현상으로부터 보호, 이물질 막기, 물 침투 보호 및 평탄하게 하는 역할.
Grinding
Back Grinding: Wafer 뒷면의 두께를 목표 두께로 연막 하는 과정으로 Lamination Tape를 부착 후 공정을 진행하여야 한다.
Stand alone type: 공정마다 따로 진행하여야 하기 때문에 장비의 이동이 필요하며, 200um 를 초과하는 경우 이 공정을 진행한다.
In line type: Remove, 웨이퍼 마운드, Back grinding을 한 장비 안에서 모두 진행 한다.
공정변수
1) Rought grinding: Wheel speed, Chuck(웨이퍼 를 올리는 판) speed, Thickness position
2) Fine grinding: Wheel speed, Chuck speed, Thickness position
3) Polishing: Chuck speed가 중요하며, Head speed, air pressure, slurry flow rate.
Wafer dicing
Wafer를 하나의 Chip단위로 분리하는 공정이다. Wafer feeding speed(웨이퍼 절삭속도, 생산량과 연관), 칼날의 높이(웨이퍼 자르는 깊이), 블레이드 회전수(생산성), 3가지 요소가 공정 변수로 작용한다.
Attach dicing tape -> Wafer dicing -> UV irradiation -> Pick up the die
*UV 과정을 통해 Tape의 접착력을 낮춘다.
Blade dicing 방법
Dicing 문제
1) Chipping(가장자리 께짐)
2) Crack
3) Debris(잔해)
4) Kerf loss(절단 손실)
5) Structural damage
6) Debris adhesion
Blade의 문제를 보완하기 위해 laser dicing방법이 있다. 약 10 배의 dicing 속도와, 물을 사용하지 않는 Dry 공정 그리고 잔해와 크랙이 생기지 않는다.
Die Attach
Chip을 Epoxy(전도성, 비전도성 물질로 접착), LOC tape, WBL tape를 이용하여 Substrate
(Lead Frame, PCB, ceramic)에 물리적으로 붙이는 과정이다. 이 공정으로 인해 Crack, Scratch, Die lifting 이슈가 생길 수 있다.
Wire bonding
Die attach 공정 이후 반도체 Chip의 전극 과 substrate의 전극을 wire로 연결해주는 공정. Heat, Pressure, Ultrasonic(초음파)가 접합에 영향을 준다.
Bump
Wire bonding의 대체하는 기술인 Flip Chip을 하기 전 공정으로 접합할 수 있도록 접합체를 만들어주는 과정이라 할 수 있다. 전극의 높이를 높이고, 외부 전극과 접속이 용이한 재료로 교체하는 역할을 한다.
UBM(Under Bump metallurgy)
범프를 형성하기 전에 본드 패드 위에 금속 층을 얇게 형성 하는 것으로, Bump 밑의 금속 층이라 하여 Under 라 한다. 잘 붙을 수 있게 해주며, 확산을 막고 충격으로부터 보호하는 역할을 한다.
Solder ball bump process
Die -> Sputter UBM -> Coat photo resist -> Expose and Develop -> Etch UBM -> Resist strip -> Add solder ball and reflow
*Resist stripping : 에칭 등의 처리가 끝난 후 코팅물 제거 공정
Plated solder bump process
Die -> Sputter UBM -> Coat photo resist -> Expose and Develop -> Plating-> Resist strip -> Etch and reflow
*애칭공정의 순서와 PR의 방식에 따라 차이가 있다.
Solder bump defect
1) Non wet open : 잘 붙지 않는 경우
2) Head in pillow : 솔더가 잘 녹지 않아 베개와 비슷한 모양을 만드는 이슈
3) Bridged joint :눌려서 다리 모양처럼 된 이슈
4) Stretched joint : 솔더 범프간에 늘어난 이슈
5) Head in pillow open : 솔더량이 부족하거나 열이 부족하여 잘 녹지 않았을 때 생기는 이슈
Underfil
밑을 매운다는 뜻의 공정으로 물리적, 화학적 충격의 내성을 확보하여 신뢰성을 향상 시킨다.
직선, ㄷ자, L, L and dot 모양 방법으로 Dispenser를 이용하여 매운다.
Molding
고온 상태의 금형에 열 경화성 수지 EMC(Epoxy Molding Compound)로 밀봉 하는 공정으로 외부 충격으로부터 와이어 본딩 된 칩을 보호하고 열의 발산 및 수분의 침투로 인한 부식을 방지한다. 즉, 외부환경의 영향과 전기적 기계적인 요소로부터 보호
*warpage : 온도 차이나 이중 물질 간의 열팽창 계수의 차이로 인하여 제품이 휘는 현상
*Smiling-Concave : 온도가 높아질 때 휘는 현상
*Crying-Convex : 온도가 급격히 낮아질 때 나타나는 현상
Solder ball attach
BGA 등의 Package 형태에서 반도체 칩과 인쇄회로기판의 패드사이에 만들어진 solder ball을 접합하여 전기적 신호가 전달이 가능하도록 하는 공정. Substrate에 잘 붙기 위해서 반드시 Flux를 바른 후 공정을 진행하여야 한다.
Solder ball Defect
1) Ball discolor : 볼의 변색(산화-전기신호가 불안정)
2) Missing ball : 볼이 제대로 붙지 않는 이슈
3) Abnormal pitch : 볼의 모양이 둥근 모양이 아닌 다른 모양을 가지는 이슈
4) Damaged ball : 볼이 손상
[MARK]반도체 칩 표면에 해당 반도체의 명칭, 제조일, 제품의 특성, 일련번호, 랏트넘버 등을 표시하여 이슈 발생시 해당 반도체를 찾아 확인하는 작업을 하기도 한다. Ink와 Laser 방식이 있다.
Singulation(Trim)
Cutting punch를 이용하여 연결부인 Dambar를 잘라 단일 Package로 분리하는 공정이다.
Singulation 공정 조건
1) Blade Exposure: 패키지 두께를 고려하여 노출 범위를 정한다. (Blade : 두께=10 : 1)
2) Dressing: Blade 표면을 매끈하게 해주는 작업
3) Kerf width: 블레이드의 크기 조절
4) Feed rate: π x Blade 지름 x RPM으로 구한다.
TEST
E/L(electrical) test: 반도체 칩에 전기적 신호를 주어 전기적 성질을 확인 즉, 반도체 내부의 스펙을 확인한다. 고온과 저온에서 테스트하여 극한 상황에서도 작동이 잘 이루어 지는지 확인. Handler 를 통하여 확인하며 Good or Reject 으로 분류 하여 준다. 약 10k/hour로 가능하다.
*상업용 25~80℃, 산업용 25~125℃, 저온 테스트는 -40℃ 까지
Tester: Handler 뒷 부분에 부착되어 반도체 칩에 전기적 신호를 주고 난 뒤 그에 맞는 value값을 측정하여, Handler에서 분류를 할 수 있게 도와주는 역할을 한다.
DUT(Device under test) card : Tester 와 반도체 칩의 pin을 연결해주는 매개체로 VDD, VTT 와 GND(접지) power supply를 가지고 있다.
Test socket: 반도체 칩과 DUT card를 연결해주는 매개체로 Pogo는 메탈로, Rubber type은 고무로 되어 있으며 컨택 수준이 pogo보다 낮아 상황에 맞게 사용하여야 한다.
MARK: test 공정 이후에도 Mark를 진행하며 Packaging 공정에서 진행한 마킹에 추가하는 마킹을 한다. DATECODE와 Part Number 등을 마킹한다
*DATECODE : 년도와 주차를 기록(Ex : 1602=2016년도 2주차), Part Number : 디바이스 특성
Scan : E/L은 내부를 확인 한 것이고, Scan은 칩의 외부, 물리적 성질을 판단한다. Check marking, Solder ball, coplanarity(공명), PCB status, Die crack
Bake: 반도체 내부의 수분을 제거하기 위한 공정으로 일반적으로 125℃에서 진행한다. Floor life를 초기화 할 때 사용한다.
*Floor life : 습도가 있는 지역에서 노출되어 있던 시간
Pack: Moisture sensitive level 을 부착하여 부품의 습도를 관리 할 수 있도록 한다(JEDEC 스펙을 기준)
HIC(Humidity indicator card): 습도의 변화를 알 수 있게 하는 카드로 Moisture barrier Bag에 packing 할 때, HIC를 함께 보관하여 습도 변화를 측정한다. 하늘색이 분홍색으로 변화하면 Bake 공정이 필요하다.
Pack: Label을 부착하여 반도체 정보를 알 수 있게 해주며 Box, tape, Reel and Tray를 통해 운반하고 보호한다.
[Lead Frame package]1) DIP (Dual inline package)
2) SIP (Single inline package) : power chip에 사용 된다.
3) ZIP : 지그재그 구조로 되어 있는 패키지
4) SOJ(Small j line) : 리드프레임이 j모양
5) LOC (Lead on chip)
QFP(Quad Flap Package): 작은 사이즈 package 적용에 용이하며 열 방출에 효율적이다. Plastic 재질사용으로 가볍다. 하지만 사이드 쪽만 사용 가능 하기 때문에 가운데 면을 사용하지 못하는 만큼 In, Out put 단자가 적다.
1) TQEP(Thin QFP)
2) LQFP: 1.4mm 두께
3) MQFP: 2mm~3.8mm일 경우
MLF(Micro lead frame): 구리 재질의 리드프레임을 사용하여 패키지 크기를 칩의 크기에 가깝게 만든 CSP 패키지 솔루션이다. 반도체 산업에서 많이 사용 되는 package기술로 제조공정이 안정적이고 제조방식 또한 안정적이다.
BGA: 이차원적 평면에 격자 형식으로 분포된 solder ball을 통하여 칩을 다음 레벨 패키지인 PCB등과 전기적으로 연결하는 것. Peripheral 형태보다 단위 package 면적당 매우 높은 수의 in, out put수를 가진다. 고성능 소자에 적합하다. 열 방출 solder ball을 칩 바로 아래 넣어 열을 방출하기 때문에 열 특성이 좋다.
PBGA: BGA에 Plastic 재질을 사용 한다. 리드 프레임 대신 PCB 기판을 사용하여 인덕턴스를 낮추고, 전기적/열 방출 능력과 표면실장성(SMT)을 대폭 향상시켰다. 하지만 Plastic 재질이기 때문에 Popcorn cracking과 같은 이슈가 있다(신뢰성 저하).
CGBA: 알루미나 세라믹 기판을 이용하여 습기를 차단하여 PBGA와 같이 수분 흡수로 인한 문제점이 적다. 환경적 문제에 안정성과 내성 등에 강하다. 하지만 무게가 무겁고 가격의 단가가 높은 단점이 있다.
CSP(Chip scale package): BGA 패키지가 발전한 패키지로 반도체 칩의 면적보다 약간 큰 패키지(반도체 칩이 전체 패키징중 80% 크기를 가진다). Solder ball과 같은 짧은 리드로 인한 인덕턴스의 감소와 개선된 전기적 성능을 가진다.
*Inductance :회로에 흐르는 전류의 변화에 의해 전자기유도로 생기는 문제
Flip chip: Wafer 에서 bare die 몰딩이 없고 외부에 노출되어 있는 경우, Die가 깨지는 이슈가 생기며 bump쪽 문제는 die를 뜯어내야 확인할 수 있다. 감춰진 연결부 문제는 x-ray장비가 필요한 단점을 가진다. 하지만 사이즈가 감소하고 기능성 증가, 성능의 향상, 신뢰성 과 열특성 향상의 장점이 있다.
Flux Dispensing(Flux 사용) -> Chip placement -> Solder Reflow -> Flux cleaning -> Underfill dispensing -> Underfill Cure 순서로 진행 된다.
FCCSP(Flip Chip Chip Scale package)
Flip chip process -> Moliding -> laser via -> via filling -> Ball attach
*Via : 두 개의 금속을 사용하는 구조에서 두 금속선을 접속시키는 매개체
WLCSP(Wafer level CSP): Wafer -> Dicing -> Packaging 순서가 아닌 Wafer -> Packaging -> Dicing 순서로 패키지 한다. Wafer의 크기가 커지고 반도체 칩 크기가 작아 질수록 더 낮은 제조 비용이 든다. 하지만 Burn in test가 필요하고 패키지의 충격 위험이 있다. 이는 Back side coating으로 완화 할 수 있다.
FOWLP(Pan out WLP): 웨이퍼 위에 일시적인 본드를 하고die를 붙여 molding후 필요 없는 부분을 제거 하는 방식. RDL칩크기를 1/16으로 만들 수 있다.
SOC: Chip 자체를 system기능을 할 수 있는 칩. 개발비용이 많이 들고 단가 또한 높다.
SIP: 여러 Chip들을 합한 것, SOC보다 짧은 시간 안에 제작 하고 제조단가가 저렴하다. SOC보다 성능은 낮으나 더 높은 성능의 칩을 개발 중이다.
COC(Chip on chip): 용량이 더 큰 메모리를 사용하는 것이 기술적으로 가능하나 높은 비용이 요구 된다. SIP의 성능과 비용 문제 해결이 필요하며 복합 DRAM(Merged DRAM) 보다 제조 비용을 크게 절감 할 수 있다.
POP
Logic과 Memory를 수직 결합해 패키지화 한 것으로, 보드 공간을 줄이고 핀 카운트를 낮추고, 시스템 통합. 그러나 시스템 통합에 한계가 있어 이중 Package 사용으로 미세한 오차와 불량품 발생 가능성이 있다. Sip 보단 시스템의 유연성과 확장성이 좋다.
TSV
반도체 Chip 적층 시 Chip들을 수직 관통하는 Via hole(미세 홀)을 형성 하여 Chip간의 전기적 신호를 전달하는 패키지 방식. Sip의 장점을 유지하며, SOC 대비 단점인 성능을 향상 시키는 것이 가능하다. Chip 간 interconnection 감소로 High density, Low power, hight speed, Thiner package 구현이 가능하다. 하지만 이종 칩 적층 시 불량 발생 가능성이 높으며 대규모 투자 비용이 필요하고 초기에는 수요의 불확실성이 존재한다.
TSV 기술 이용에 따른 효율적인 Wafer 이용
1) 단위 칩 면적 감소 필요 : 웨이퍼에 보다 많은 반도체 칩을 집적하기 위한 기술
2) TSV 기술로 반도체 칩 영역을 최소화 하여 Wafer 내에 가용 칩 개수를 늘릴 수 있다.
3) 이중 소자 끼리 접합이 가능
TSV 기술 특징
저전력 + 고성능 +경박단소, TSC는 기존 POP대비 35% 패키지 기를 축소할 수 있고, 전력소모는 POP대비 50%, Bandwidth는 8대 개선 할 수 있다.
*Bandwidth : 대역폭, 이 값이 크다면 같은 속도 대비 더 많은 Data 전송 가능
Via First and Via last
1) Via First: TSV 를 반도체 COMS 공정 이전에 형성
a) 폴리 실리콘 등을 전도체로 사용(구리와 같은 금속류 사용 하지 못한다)
b) 낮은 전도도로 제한적 인터커넥션
c) Cell Stack (3D Nand Flash)
CMOS + BEOL -> Vias -> Thinning -> Bonding
2) Via last : TSV를 Fab 의 BEOL 공정과 Bonding 이후에 진행하는 방식
a) 후공정 업체들이 웨이퍼를 받아서 TSV Package 구현 가능
b) CIS에 사용하는 방식
c) Dio to Wafer 또는 Wafer to Wafer 방식 (B2F)
*CIS : 이미지 센서
CMOS + BEOL -> Bonding -> Thinning -> Vias
728×90
반응형
반도체 후공정 – 테스트(Test)공정
728×90
반응형
Test 공정
반도체 후공정에서 이뤄지는 테스트(Test)란, 전기적 특성 검사를 통해 웨이퍼나 칩의 불량이 다음 공정으로 넘어가지 않도록 방지함으로써 손실을 최소화하는 공정입니다. 초창기의 테스트는 양산 제품에 대해 불량을 걸러내는 필터링 위주로 진행했으나, 최근에는 테스트 결과의 누적된 사례를 기반으로 신뢰성 불량을 사전 차단하고, 수율을 향상해 원가 절감에 기여하는 역할까지 포괄하고 있다.
■ 반도체 테스트 공정 FLOW
반도체 테스트 공정 흐름도(사진-SK 하이닉스)
수많은 공정을 거쳐 제작된 반도체는 각 공정이 제대로 수행했는지 검증하기 위해 상온(섭씨 25도)에서 테스트를 진행합니다. 테스트는 크게 Wafer Test, Package Test, Module Test로 이뤄집니다.
고온과 저온에서 실시하는 신뢰성의 일종인 Burn-in/Temp Ctclimg 공정의 경우, 초창기에는 Package Test 공정에만 실시했지만 점차 Wafer Test 공정의 중요성이 높아져 Package Burn-in 항목이 다수 WBI(Wafer Burn-in)으로 옮겨졌습니다. 테스트와 Burn-in을 결합한 TDBI(Test During Burn-in) 개념으로 Burn-in을 진행함에 따라, 정식 테스트를 Burn-in 전후에 실시하는 복합형도 많이 활용되는 추세입니다. 이렇게 되면 공정 시간과 비용이 절약될 수 있습니다.
테스트 공정은 IDM/Foundry가 직접 수행하기도 하고, 일정 부분을 위탁업체(OSAT; OutsourcedSemiconductor Assembly and Test)에 외주를 주기도 합니다. 테스트 공정의 주체가 누구든지 동일한 검사 장비와 검사용 부품을 사용해 테스트하게 됩니다.
■ 반도체 테스트의 목적
반도체 테스트의 목적은 불량칩을 골라내고, 전공정들을 점검해 개선하는 것을 목적으로 합니다. 이 과정에서 다음 공정으로 불량칩이 넘어가 지 못하게 하는 선별률은 항상 중요한 이슈입니다.
원가점감 및 수익 향상
New Tech 확보와 수율 향상
초기, 중기 불량 선별 목적
반도체 기술 및 제품의 연구, 개발 개선
반응형
■ 반도체 테스트 종류(공정 측면)
반도체 테스트는 공정은 Wafer Test, Package Test, Module Test로 구분할 수 있으며, 기능별로 구분할 경우 DC(Direct Current)/AC(Alternating Current)/Function/실장/신뢰성 테스트 등으로 나눌 수 있습니다.
반도체 테스트 공정측면 흐름도(사진-SK 하이닉스)
■ Wafer Test
전공정이 끝난 웨이퍼에 대한 성능 및 품질 테스트를 하는 단계입니다. 테스트 과정은 크게 Burn-in 테스트, 프로브 테스트, 리페어(Repair) 공정으로 이뤄집니다. Burn-in 테스트는 사용자인 고객이 장기간 사용하는 정도의 스트레스 상황을 조성해 불량이 발생할 수 있는 요인을 사전에 확인하는 작업입니다. 프로브 테스트는 웨이퍼 상태에서 소자의 전기적 특성을 확인하는 과정입니다. 웨이퍼에 프로브카드를 통해 전기적 신호를 가하면서 소자의 정상 작동 여부를 확인하는 과정입니다.
■ Package Test
패키징 공정이 끝난 후 제품을 출하하기 전 최종적으로 전기적인 특성을 검사한다고 하여 파이널 테스트(Final Test)라고 부릅니다. Package Test는 가장 중요한 테스트 공정으로써 모든 테스트 항목이 집중돼 있습니다. 먼저 DC/AC 테스트와 Function 테스트에서 양품(Go)/불량품(No-Go)을 판정한 뒤, 양품들 중 속도별로 그룹을 가르는 Speed Sorting(ex. DRAM)을 진행해 고객이 요구하는 속도를 만족하는 제품을 확보합니다.
■ Module Test
PCB에 8~16개의 칩을 탑재한 후 진행한다고 하여 보드 테스트(Board Test)라고도 합니다. Module Test에서는 DC/Function 테스트 후 실장 테스트를 진행, 되도록 고객이 실제 제품을 사용하는 환경에서 칩을 선별할 수 있도록 합니다. 이 과정에서 불량 칩이 발견되면 양품 칩으로 교환해 새롭게 모듈을 구성할 수 있습니다.
■ 반도체 테스트 종류(기능 측면)
■ DC Test
반도체 테스트는 공정은 Wafer Test, Package Test, Module Test로 구분할 수 있으며, 기능별로 구분할 경우 DC(Direct Current)/AC(Alternating Current)/Function/실장/신뢰성 테스트 등으로 나눌 수 있습니다.
■ AC Test
AC Test는 시간 변수에 따른 입력이 주어졌을 때 Signal의 Set-up Time, Hold Time 등 Time 관련 사항을 주로 점검하고 제품의 동작 시간을 측정하며, 이를 통해 DRAM 단품 같은 경우, 속도별로 담아 놓는 통(Bin)을 마련해 분리해내는 Bin-Sorting를 실시합니다.
■ Function Test
Function Test에서는 칩의 패드에 여러 종류의 테스트용 패턴(혹은 Vector Data)을 인가해 제공된 Truth Table과 일치되는 결과를 도출하는지를 점검합니다. 이는 단일 소자가 아닌 여러 소자(Column/Row 혹은 Block)를 한꺼번에 점검함으로써 간섭 현상이나 누설전류 등으로 인해 주변 Tr에 어떠한 영향을 끼치는지 등을 확인합니다.
반도체 제품의 테스트는 테스트 관점과 방법이 매우 다양하며, 또한 공정 효율성을 높이고 비용을 낮추기 위해 패키지 레벨 테스트와 웨이퍼 레벨 테스트 항목을 교환하기도 하며 각 공정에 맞게 변화를 주기도 합니다. 이러한 복합적인 요인을 맞추기 위해 기업들은 제품 설계에서 장비 및 공정, 테스트 방법까지 포함한 모든 공정의 제품 개발을 지속적으로 하고 있습니다.
728×90
반응형
Package Test
‘TEST’하면 보통 ‘시험’이라는 의미로 생각하기 쉬운데, 반도체 제조공정에서 TEST란 『검사』의 개념이 강합니다.
즉, 제대로 된 양품인지 아니면 불량인지를 선별하는 공정을 말하는 것이지요.
반도체 TEST 공정은
웨이퍼 완성 (chip) 단계에서 이루어지는 EDS TEST, 조립공정을 거쳐 Package화 된 상태에서 이루어지는 Package TEST, 출하되기전 Customer 관점에서 실시되는 QA TEST 등 여러 단계에 걸쳐 이루어집니다.
구 분 특 징 비 고 EDS Electrical Die Sort의 약자
웨이퍼 상태의 chip이 양품인지 불량인지만 선별
Grade (등급) 구분 안함
PACKAGE TEST EDS 공정에서 양품으로 판정받은 chip만 조립공정을 거쳐Package 형태로 만든 후에최종 불량유무를 선별하는 것으로 Final Test 라고도 함
양품은 성능에 따라 등급 구분
QA TEST 입고 검사 Test
출하될 제품중 sampling하여품질의 이상유무를 Customer의 관점에서 검사
Package Test란 일련의 제조공정 (회로 설계 → FAB → EDS → Ass’y)을 거쳐 탄생한 패키지를 씌운 반도체 TEST 조건이 입력된 컴퓨터 (TESTER)를 통해 전압이나 Signal (전기 신호), 온도 등의 Stress (자극)를 가함으로써, 제품의 전기적 특성, 기능적 특성 및 제품의 동작 속도 등을 신속히 검사하여 양품과 불량을 구별하는 공정입니다.
· Test 진행중 발생되는 Data를 수집, 분석하여 제품의 특성적인 변화를 판단하고 필드 불량에 대응하며
· Test 결과를 FAB 및 Ass’y 공정으로 Feedback 함으로써 제품의 특성 및 수율을 향상시키기 위해 진행됩니다.
※ 반도체는 제품별로 각기 다른 PKG TEST FLOW를 거치게 되는데 이 단원에서는 메모리(DRAM)를 기준으로 살펴보기로 하겠습니다.
조립공정을 거치면서 발생된 불량을 걸러내는 단계 (상온에서 test) 제품의 초기불량을 미리 제거하기 위해 고온 (125℃)에서 일정 시간 제품에 스트레스 (Vcc)만 가해줌 Burn-In에서 설비 문제로 생긴 Reject sample을 다시 RUN 구성 상온 및 Cold (25℃~-5℃)에서 취약한 제품을 선별하는 단계 고온 (75~83℃)에서 이루어지는 공정으로 Hot-final 공정이라고도 하며 speed별로 제품이 구분됨 제품의 특성을 확인할 수 있도록 다양한 제품정보 표시 패키지 외관검사 제품 포장
TEST란 Tester 설비를 이용하여 만든 Program을 통해 Burn-In 공정 이후 Device의 초기불량 및 Hard성 불량 , 전기적 특성, 기능 등을 중심으로 검사하는 공정으로 BURN-IN 공정 이후 실질적인 Device의 Test가 이루어집니다.
완제품 패키지의 전기적 특성 및 기능을 TEST하는 항목은 크게 DC Parameter TEST와 Dynamic Functional TEST로 구분됩니다.
DC Parameter TEST
– Chip의 전기적 특성을 측정하는 TEST로 ·Contact TEST (Open/Short TEST), ·Leakage TEST (입출력 Pin) ·Current TEST (Standby / Operation
Current) 등이 진행되니다.
Dynamic Functional TEST
– 모든 Cell이 정상적으로 동작하는지 즉 Device의 Operating 기능을 TEST하는 것으로 TIMING Parameter, In/Output Signal Level, Address Enable
방법, Scramble, Pattern 등을 통해 TEST합니다.
이외에도 ……
SPEED SORT 검증 TEST
– Device 동작시 Timing Parameter (Device를 동작시키 위한 Timing 조건)를 이용한 Device의 실질적인 Speed를 구분합니다.
LOW POWER TEST – Device 동작시 소모되는 전류, Data의 저장 능력에 의한 Refresh 주기 등을 검증하여 Device의 소모전력을 구분짓는 Normal & Low Power 제품으로 구분 TEST하는 것으로 나눌수 있습니다.
이때 Device는 Sampling 검사가 아닌 생산 Device 전량 검사합니다.
조립이 완료된 Device를 TEST하기 위한 첫 단계는 INPUT GATE로써 Device Type, 수량, I/O수 (Bit수) 등을 확인하여 TEST용 Lot Card를 작성하는 공정입니다.
Lot Card는 제품이 거치게 되는 모든 공정 flow와 시간, YIELD (수율), 작업자, 사용 프로그램 등이 기록될 Sheet로써 입고시까지 Device와 함께 흘러가고 Device 입고 후에도 일정기간 보관됩니다.
FAB 및 조립 공정을 거치면서 발생된 불량 Device를 걸러내는 공정으로 특히 어떠한 Test조건에서도 Device가 전혀 동작하지 않는 완전한 불량 즉, Device의 Hard성 불량 및 전기적 특성 불량을 중점적으로 TEST합니다.
이는 전기적 특성이 불량인 디바이스가 BURN-IN 공정 진행시 Good Device (양품)에 Damage를 주는 것을 방지하기 위해 진행됩니다.
TEST 온도는 25℃ 상온 (Room Temp.) 으로, 특히 고온에서 보다 저온에서의 특성이 약한 불량을 Screen 해냅니다.
Burn-In 완료후 Good & Reject을 선별하는 공정이 Unloading 입니다.
BURN-IN이란?
일반적으로 Device (패키지 형태로 완성된 제품을 디바이스라고 함) 는 보통 1,000시간 안에 불량 이 발생할 확률이 가장 높은데, 이 때 발생하는 불량을 초기불량 이라 합니다.
BURN-IN이란 이처럼 초기에 발생할 수 있는 제품의 불량을 미리 제거하기 위해 제품에 어떤 극한 조건을 가해줌으로써 제품의 초기불량을 유도, 살아남는 Device만을 걸러내는 공정입니다.
극한 조건이란 일반적으로 높은 Voltage (전압), 고온 (140℃ 정도), Signal (전기 신호) 등의 Stress를 가하는 것을 말하는데, 디바이스에 따라 Stress 조건은 약간씩 다르게 설정됩니다.
이러한 과정을 통해 반도체 제품이 PC 및 전자기기 등에 탑재되어 장시간 무리없이 동작할 수 있는 신뢰성을 확보하게 됩니다.
cf) Wafer 완성 단계에서 불량 여부를 판단하는 EDS 공정에서도 이와 유사한 공정이 진행됩니다.
* ILT : Infant Life Test 초기수명 시험 (신뢰성)
Burn-In Stress에 의하여 발생되는 초기불량의 재현을 위한 실험단계로 추가 Burn-In을 실시하여 제품의 신뢰성을 향상 Burn-IN의 목적
불량 Device를 발견하고 교체하는데 소요되는 시간과 경비는 각 생산 단계마다 크게 증가하므로 초기에 불량 발생 가능한 Device를 Field에 공급되기 전에 걸러내어 불량 수리에 대한 전체 비용을 절감할 뿐만 아니라 Device의 Field 품질을 높이는데 결정적인 기여를 하는 것입니다.
Burn-In의 종류
BURN-IN은 Signal 인가방식에 따라 STATIC 방식 과 DYNAMIC 방식 으로 구별됩니다.
Burn-In 방법
Burn-In의 한 방법으로 정상적인 조건에서 1,000시간 동안 Device를 동작 시킨후 각 Device들의 기능을 Test하는 Stress Test 방법이 있습니다.
반도체의 불량은 온도가 증가함에 따라 가속화 된다는 것은 잘 알려진 사실입니다.
동일한 전압이나 전기 신호를 상온과 고온에서 똑같이 가했을 때 고온에서의 초기불량 발생이 상온의 경우보다 증가되므로 TEST 상황에서 온도를 증가시킴으로써 Burn-In 시간을 줄일 수 있습니다.
Temperature (℃) 25 70 125 240 Time (HRS) 1000 310 36 4
Burn-In 온도와 시간과의 관계
Failure Process를 가속시키기 위한 방법으로써 Device의 Power Voltage 를 올리기도 합니다.
즉 Device의 Power Voltage를 보통보다 10%정도 높은 Voltage Stress를 가하는데 이는 반도체 Insulator Breakdown과 표면 효과로 인한 Failure Process를 가속 시키기 때문입니다.
그러나 앞서 설명한 Stress에 의한 Failure Process를 가속시켜 Burn-In Time을 단축하는 데는 사실 한계가 있습니다.
즉 온도 900℃와 Voltage 인가를 9V(Device Operating Voltage : 5V 인 경우)로 Stress를 주었을 경우 Burn-Time을 최소화 할 수는 있으나 이러한 경우는 과다 Stress로 인하여 정상적인 Device동작 조건에서는 발생하지 않는 Fail을 유발시키게 되므로 Stress 조건에 대해서는 충분한 검토가 필요합니다.
MBT 공정이란 Monitoring Burn-in & Tester의 약자로써 DYNAMIC SYSTEM의 AGING 능력과 TESTER의 TESTING 능력을 함께 갖춘 장비를 말하는 것으로 AGING TIME이란, MEMORY DEVICE에 열적, 전기적 악조건을 가하는 프로세스를 말한다.
MBT의 종류에는 1,2 ZONE으로 구성된 PROFIT1300S와 1,2,3 ZONE으로 구성된 PROFIT1000S의 2가지가 있다.
RISING TIME : 온도 상승 시간
BURN-IN하는 온도까지 상승 후 COOLING 시키기 전까지의 시간 (BURN-IN)
COOLING TIME : 온도 하강 시간
TEST TIME : HOT TEMP.에서 행해지는 TEST
ROOM TEMP TEST : 25℃ (상온)에서 행해지 는 TEST
MBT test 완료 후 Unloading time 종래의 Burn-In 방식은 Stress (전압, 온도, 시간 등) 만을 가한 후 Device의 양품과 불량품의 구분은 Test 공정에서 모두 판별 하였으나 MBT의 도입으로 인하여 Burn-In 이후 동일 Burn-In 시스템에서 일부 Long Cycle Item에 관하여 디바이스의 양품과 불량을 Test할 수 있게 되었습니다.
즉 기존의 Dynamic Burn-In 장치에 출력판정용 Tester 기능을 추가한 것이 Monitoring Burn-In 입니다.
따라서 Monitoring Burn-In을 실시하게 됨으로써
Tester에서의 측정시 시간이 과다하게 소요되는 Long Cycle Item을 Aging (B/I공정) 중에 실시함으로써 Test 공정의 Capa를 크게 향상 시킬 수 있었으며
불량 Device의 불량 Mode 또는 불량 Address의 해석도 자동적으로 이루어 짐으로써 불량분석 기간을 단축할 수 있고
진행성 Recover 불량 Mode의 검출로 인하여 Field의 품질불량을 한층 강화할 수 있습니다.
B/I직후에는 불량을 유발하나 차츰 시간이 지연됨으로써 불량이 Recover 되는 Device의 검출로 인하여 Field의 품질불량을 한층 강화할 수 있습니다.
SIGNAL의 이해
Signal이 Low( Vil )에서 Hihg( Vih )로 올라 가는데 걸리는 시간
( 10%~90% )
Signal이 High에서 Low로 내려오는데 걸리는 시간
( 90%~10% )
펄스(Signal)의 파형이 상승시점에서 정상값을 유지 하지 못하고 잠시 진동하는 현상
Signal의 파형이 하강할때 기준선을 유지하지 못하고 기준선 이하로 내려가며 잠시 진동하는 현상
일반적으로 Post-Burn TEST는 Room Temp. (상온, 25℃) 이하에서 Device의 전기적 특성 및 기능을 TEST 하며, Burn-In의 Stress에 의해 발생된 초기불량을 걸러내는데 Speed 별로 구분하지는 않습니다.
이 공정에서 발생된 불량은 전량 Scrap 처리하며 양품에 한하여 다음 Step인 Final TEST를 진행합니다.
TEST 되는 온도 조건에 따라서 각각 Post-Cold, Post-Cool, Post-Room 으로 불리워 지기도 하지만 일반적으로는 Post-Burn TEST라고 합니다 Post Test의 Temp.환경이 일정한 것이 아니고 제품에 따라 Temp.의 환경이 Cold (-5’C), Cool (5’C), Room Temp. (25℃) 에서 Test 되기 때문이지요.
또한 최근에는 특정 Customer로부터 Industrial (-40’C), 또는 Extended (-25’C)에서의 Test를 요구하는 경우도 많이 있으며 이 경우는 System의 Temp.능력을 감안하여 엔지니어의 분석에 의하여 Cool (5’C) Temp에서 대응할 수 있도록 Correlation 이 진행되고 있습니다.
현재 Data Book에서 제시하는 AC/DC Parameter 의 Temp. 수준은 0℃ ~ 70℃이나 Device의 품질 및 특성을 고려하여 초기 신제품의 경우 에는 Cold Test (-5’C)를 진행하고 있습니다.
상온 및 저온에서 행해지는 Post-Burn TEST를 무사히 통과한 반도체들은 이번에는 고온에서의 시련을 견뎌야 진정한 반도체로 탄생합니다.
Final TEST는 고온에서의 Device의 전기적 특성, 기능을 검사하는 공정으로 FINAL-HOT 이라고도 하는데 제품이 갖는 전기적, 기능적인 특성들을 75℃에서 검사하여 제품의 Speed 및 Function 불량 등을 BIN으로 구분하는 공정입니다.
BIN이란 양품의 제품을 Speed별로 구분하기 위하여 사용하며 또한 유사한 불량 유형을 갖는 Fail (불량) 제품을 유형별로 묶어 분석을 빠르고 쉽게 할 수 있도록 TEST 프로그램에서 나눕니다.
여기서 구분되는 Data를 이용하여 이 후의 MARKING 공정에서 User가 알아볼 수 있도록 Speed를 결정하는데 이 공정이 TEST 시간도 가장 많이 걸립니다.
Hot Temp 온도 조건은 90%이상 제품이 75℃에서 Test를 진행하고 있으며 최근에는 Junction Temp . 관련하여 업체의 요구가 계속되고 있어 이를 수용하기 위한 Junction Temp.의 분석업무가 진행되고 있습니다.
품질을 안정적으로 유지하기 위해 Spec에 제시된 것보다 고온에서 FINAL TEST하고 있습니다.
또한 Hot Temp. 조건에서 Speed가 Delay 되는 점을 감안하여 실제 Speed Bin Sorting이 이루어 지고 있습니다.
FINAL-HOT TEST에서 발생되는 불량은 전량 Scrap처리하고 양품에 한하여 다음 Step인 Marking을 진행하여 입고, 출하됩니다.
* BACK-END 공정
Back-End 공정이란 TEST 공정의 마무리 단계로 Marking, Auto Inspection, Packing 공정을 총칭하는 말로써 MVP 공정이라고도 합니다 .
MARKING공정이란? 여러가지 TEST 악조건을 꿋꿋이 견뎌낸 패키지들만이 자신의 이름을 갖게 되는데 이것이 바로 Marking 공정입니다.
패키지 위에 제품의 기능이나 특성을 나타내는 Bit수, Speed, Power 및 동작 Voltage, PKG TYPE, 제조국가, 제조일 등 제품에 대한 이력을 기록함으로써 Customer는 표면에 Marking되어 있는 Code만 보아도 제품에 관한 정보를 한눈에 읽어 읽어 낼 수 있습니다. Marking 이란 상품의 얼굴이라 할 수 있으므로 완벽하게 마무리 될 경우 Customer로 하여금 제품에 대한 신뢰도를 한층 높일 수 있게 됩니다. 종류
– Marking의 종류에는 Ink Marking과 Laser Marking으로 구분되는데 최근에는 선명한 Laser Marking이 주로 사
용되고 있습니다. ① MASK 방식의 YAG PULSE LA MASK의 LASER 및이 조사되는 부분의 순간 증발로 표면을 제거하는 방식
② PEN & SCANNING 방식의 YAG CW LASER
LAMP가 ON 상태에서 LASER PULSE 폭을 O-SWITCH라는 일종의 SHUTTER로 조정하는 방식 MARKING CODE 예
AUTO INSPECTION이란?
– 제품의 출하에 앞서 Marking 상태, Bent Lead 등 패키지 외관이 손상되었는지 여부를 확인하는 공정으로, CCD Camera 및 Laser를 이용하여 제조공정에서 발생할 수 있는 여러 가지 제품의 외관불량을 Packing 입고 전에 자동으로 Screen하는 공정입니다. 종류
보통 불량 항목은 크게 Lead 관련 불량 과 패키지성 불량 , Marking성 불량 으로 구분되며 육안검사와 자동검사가 있는데 육안 검사는 최근 Monitoring으로 전환하고 대신 Auto Inspection 설비로 전량 자동검사를 실시하고 있습니다. 설비로는 Lead 불량과 Marking 불량을 검사하고 있으며 Lead 불량이 발생하였을 경우에는 Reformer라는 Lead 교정 설비로 Rework을 실시합니다.
종류 Check Point AUTO-INSPECTION BENT LEAD, MARKING 상태 MONITORING CRACK, SCRATCH, 변색, MOLDING 불량
검사 항목
Auto Inspection 공정을 통해 PKG 외관을 check 합니다.
① Coplanarity (편평도)
Device가 평면에 위치하였을 때를 기준으로 하여 상대적으로 Lead가 들뜬 정도
② Pitch (Lead Bent)
Lead 중심에서 인접된 두 Lead 중심간의 간격
③ Terminal Dimension
마주보는 한쌍의 Lead 끝에서 끝까지의 거리.
④ Width : Lead의 폭
⑤ Gap : Lead와 Lead 사이의 간격
⑥ SKEW : Device의 Lead가 원래의 기준점에서 벗어난 정도
※ QA GATE
제품이 입고 되기 전 일부를 Sampling하여 전기적 특성과 외관검사를 품질보증 차원에서 GATE 성격으로 진행하여 입고 여부를 판정하는 공정으로 이 때 AQL Level을 적용하여 입고 여부를 판정하고 불합격시 Sampling된 LOT 전체를 TEST 공정으로 돌려보내 다시 TEST하게 합니다.
자세한 사항은 QA 단원에서 살펴보기로 하겠습니다.
PACKING공정이란?
Packing이란 모든 검사가 완료된 후 제품출하에 앞서 입고를 하기 위한 단계로 제품을 습기 및 충격으로부터 보호하기 위한 포장작업 을 말합니다. 방법
Packing의 방법으로는 제품 포장용 Bag인 Shielding Pack을 이용한 Dry Packing 과 Carrier Tape에 Device를 담아 Cover Tape로 밀봉하고 Reel에 감아 출하하는 Tape & Reel Packing 이 있습니다.
특히 Surface Mount Device (SOJ, TSOP,QFP 류)의 제품은 PCB 실장시 순간적으로 고온상태에서 작업이 진행되므로 습기에 의한 패키지 Crack이 발생 할 수 있어 이를 방지하기 위하여 Tape & Reel이란 자재에 Packing 하여 방습포장을 합니다. [관련 용어]
SOAK TIME
Soak Time이란 Device를 Cold 또는 Hot Temp. 조건에서 Test하고자 할 때 원하는 온도를 맞추기 위하여Handler 내부의 Pre Heater에서 일정한 온도를 가한뒤 Test Site로 가서 Test를 하게 되는데 이 때 걸리는 시간이 Soak Time 입니다. INDEX TIME
Index Time이란 Device의 TEST가 완료되어 Sorting한 후 다음 Device를 동시 TEST하기 위하여 모든 Dut(Socket)에 Device가 이동하여 TEST 를진행하기까지의 대기시간을 Index Time 이라고 한다. TEST TIME
Test Time이란 Device의 순수 Test Time과 Test 대기시간인 Index Time을 합한 시간을 말합니다.
따라서 한 대의 설비에서 시간당 생산할 수 있는 Capa 산출에 중요한 기본 요소가 됩니다. TESTER INTERFACE Tester Interface란 Tester와 Handler간의 정보를 서로 주고 받는 내용으로 통신사양은 RS-232방식 (직렬방식)과 GPIB방식(병렬방식)이 있으나 최근 GPIB방식으로 전환 되고 있습니다.
키워드에 대한 정보 반도체 테스트 공정
다음은 Bing에서 반도체 테스트 공정 주제에 대한 검색 결과입니다. 필요한 경우 더 읽을 수 있습니다.
이 기사는 인터넷의 다양한 출처에서 편집되었습니다. 이 기사가 유용했기를 바랍니다. 이 기사가 유용하다고 생각되면 공유하십시오. 매우 감사합니다!
사람들이 주제에 대해 자주 검색하는 키워드 반도체 테스트 공정, 6분만에 이해시켜드립니다!!
- 반도체
- 후공정
- 테스트공정
- 프로브카드
- 포고핀
- 러버타입
- 6분투자
반도체 #테스트 #공정, #6분만에 #이해시켜드립니다!!
YouTube에서 반도체 테스트 공정 주제의 다른 동영상 보기
주제에 대한 기사를 시청해 주셔서 감사합니다 반도체 테스트 공정, 6분만에 이해시켜드립니다!! | 반도체 테스트 공정, 이 기사가 유용하다고 생각되면 공유하십시오, 매우 감사합니다.