당신은 주제를 찾고 있습니까 “선택적 레이저 용융 – Laser 3d sls“? 다음 카테고리의 웹사이트 https://you.charoenmotorcycles.com 에서 귀하의 모든 질문에 답변해 드립니다: https://you.charoenmotorcycles.com/blog. 바로 아래에서 답을 찾을 수 있습니다. 작성자 Timo Roininen 이(가) 작성한 기사에는 조회수 19회 및 좋아요 없음 개의 좋아요가 있습니다.
선택적 레이저 용융 주제에 대한 동영상 보기
여기에서 이 주제에 대한 비디오를 시청하십시오. 주의 깊게 살펴보고 읽고 있는 내용에 대한 피드백을 제공하세요!
d여기에서 Laser 3d sls – 선택적 레이저 용융 주제에 대한 세부정보를 참조하세요
선택적 레이저 용융 주제에 대한 자세한 내용은 여기를 참조하세요.
선택적 레이저 용융 | HiSoUR – 안녕하세요.
선택적인 레이저 용융으로, 분무 화 된 미세 금속 분말의 얇은 층은 수직 (Z) 축으로 움직이는 인덱싱 테이블에 고정 된 기판 플레이트, 일반적으로 금속에 코팅 메커니즘 …
Source: www.hisour.com
Date Published: 12/4/2022
View: 2991
선택적 레이저 용융 공정의 공정변수 평가를 위한 용융풀 유한 …
선택적 레이저. 용융(Selective Laser Melting, SLM)은 PBF 방식의 적층. 제조 기술 중 하나로, 복잡한 형상의 금속 부품을 높. 은 효율성과 정밀도로 성형할 수 있어 최근 …
Source: jkimst.org
Date Published: 4/17/2022
View: 1338
선택적 레이저 용융법으로 제조한 316L 스테인리스강의 기계적 …
층 제조 기술 중 하나인 선택적 레이저 용융법(SLM: selective laser melting)은 높은 정밀도와 자유도를 지닌다. [1-4]. 해당 공법은 분말 공급 장치에서 일정한 면적을 …
Source: www.koreascience.or.kr
Date Published: 3/7/2021
View: 9063
Ti-6Al-4V 금속 분말에 의한 선택적 레이저 용융법 수치 해석
선택적 레이저 용융법(SLM: Selective Laser Melting)은 3D 프린팅 기술의 하나로 최근 주목 받고 있습니다. SLM에서는 레이저 조사 중 높은 온도 구배로 인해, 용융과 …
Source: flow3d.co.kr
Date Published: 3/3/2021
View: 8218
NAVER Academic > 선택적 레이저 용융 3D 프린팅 공정과 …
따라서 형상에 제한이 거의 없는 선택적 레이저 용융(Selective Laser Melting, SLM)방식 의 금속 3D 프린팅 공정을 도입하여 소수성을 띄는 금속표면 제작을 하였다.
Source: academic.naver.com
Date Published: 10/3/2022
View: 1433
산업용 선택적 레이저 용융 SLM 3D 프린터 및 서비스 및 …
선택적 레이저 용융 (Selective Laser Melting, SLM)은 고출력 레이저를 사용하여 금속 분말을 융합 및 융합시키는 특수 프로토 타입 제작, 3D 인쇄 또는 첨가제 제조 …
Source: ko.3dprotofab.com
Date Published: 6/18/2022
View: 1750
선택적 레이저 용융 방법으로 제작한 치과용 코발트 크롬 합금에 …
선택적 레이저 용융 방법의 공정 중 급속 가열과 냉각 과정은 제작된 합금의 미세구조와 결정립을 미세화하고, 기포를 감소시켜 기존 제작 방식에 의한 합금에 비해 기계적 …
Source: scienceon.kisti.re.kr
Date Published: 7/23/2022
View: 8380
주제와 관련된 이미지 선택적 레이저 용융
주제와 관련된 더 많은 사진을 참조하십시오 Laser 3d sls. 댓글에서 더 많은 관련 이미지를 보거나 필요한 경우 더 많은 관련 기사를 볼 수 있습니다.
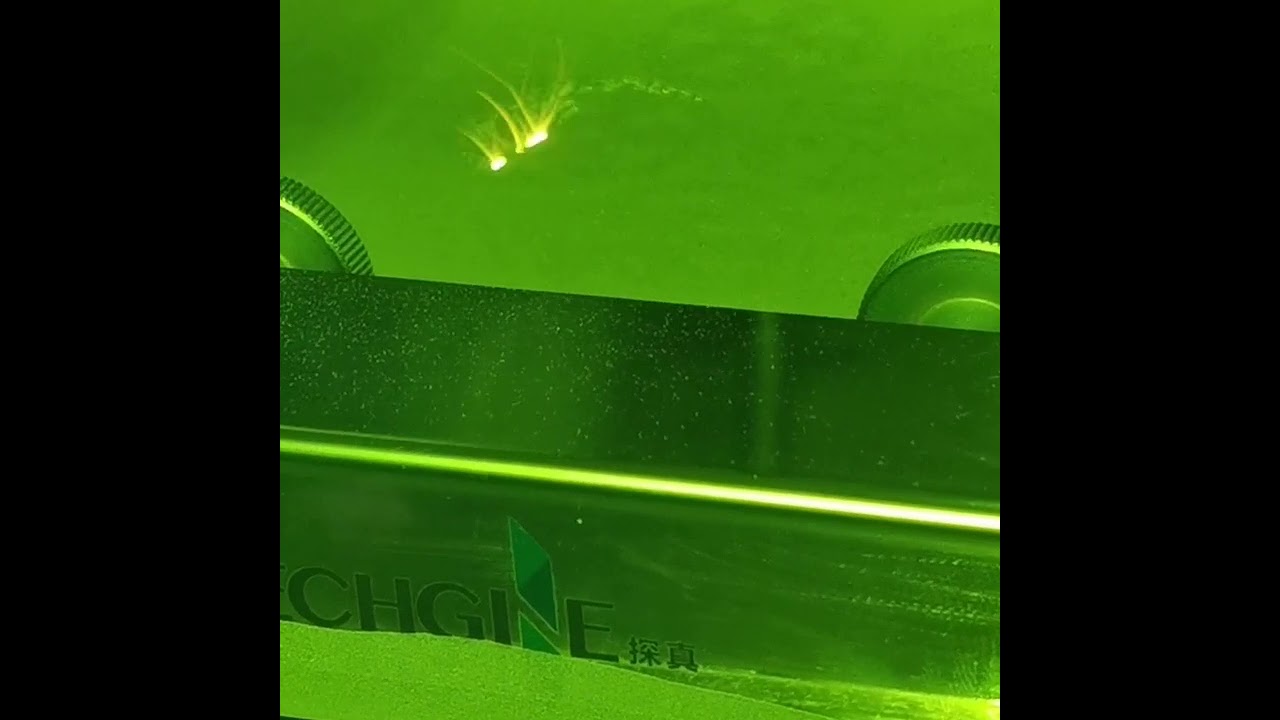
주제에 대한 기사 평가 선택적 레이저 용융
- Author: Timo Roininen
- Views: 조회수 19회
- Likes: 좋아요 없음
- Date Published: 2022. 1. 7.
- Video Url link: https://www.youtube.com/watch?v=e16Qa2q7uqg
선택적 레이저 용융 – HiSoUR – 안녕하세요.
선택적 레이저 용융 (SLM) 또는 직접 금속 레이저 소결 (DMLS)은 고밀도 레이저를 사용하여 금속 분말을 융합 및 융합시키는 고속 프로토 타이핑, 3D 인쇄 또는 첨가제 제조 (AM) 기술입니다. 많은 SLM에서 선택적 레이저 소결 (SLS)의 하위 범주로 간주됩니다. SLM 공정은 금속 재료를 SLS와는 달리 3 차원 입체 부품으로 완전히 녹일 수있는 능력이 있습니다.
역사
독일의 아헨 (Aachen)에있는 프라운호퍼 연구소 (Fraunhofer Institute) ILT에서 1995 년에 시작된 선택적 레이저 용융은 소위 기본 ILT SLM 특허 DE 19649865로 이어진 독일 연구 프로젝트로 시작되었습니다. 이미 선구적인시기에 Dr Paderborn에 소재한 F & S Stereolithographietechnik GmbH의 Dieter Schwarze 박사와 Matthias Fockele 박사는 ILT 연구자 Dr. Wilhelm Meiners 박사와 Konrad Wissenbach 박사와 협력했습니다. 2000 년 초 F & S는 독일 북부의 Luebeck에 위치한 MCP HEK GmbH (이후 MTT Technology GmbH, SLM Solutions GmbH)와 상업적 제휴를 체결했습니다. 최근 Dieter Schwarze 박사는 SLM Solutions GmbH와 공동으로 Matthias Fockele 박사가 Realizer GmbH를 설립했습니다.
ASTM International F42 표준위원회는 선택적인 레이저 용융을 “레이저 소결”범주로 분류했다. 비록 이것이 사실 인 선택적인 레이저 소결 (SLS)과는 달리 고체가 균일 한 물질로 금속을 완전히 녹이기 때문에 잘못된 명칭이다. 소결 공정. 선택적 레이저 용융의 또 다른 이름은 직접 금속 레이저 소결 (DMLS)입니다.이 이름은 EOS 브랜드에서 입금되었지만, 실제 가공 과정에서 오해의 소지가 있습니다. 생산 중에 소결되지 않고 부품이 완전히 밀집되어 있기 때문에 오해의 소지가 있습니다. 이 프로세스는 모든 시점에서 다른 SLM 프로세스와 매우 유사하며 종종 SLM 프로세스로 간주됩니다.
비슷한 과정은 전자빔을 에너지 원으로 사용하는 전자빔 용해 (EBM)입니다.
순서
선택적 레이저 용융에서, 처리 될 재료는베이스 플레이트상의 얇은 층에 분말 형태로 도포된다. 분말 형 물질은 레이저 방사선에 의해 국부적으로 완전히 재 용융되고 응고 후 고체 물질 층을 형성합니다. 이어서,베이스 판을 층 두께만큼 하강시키고 분말을 다시 도포한다. 이주기는 모든 층이 재 용융 될 때까지 반복됩니다. 완성 된 구성 요소는 여분의 파우더로 세척하거나 필요에 따라 처리하거나 즉시 사용합니다.
구성 요소의 구성에 일반적으로 사용되는 층 두께는 모든 재료에 대해 15 ~ 500 μm입니다.
레이저 빔 유도를위한 데이터는 3D CAD 바디의 소프트웨어를 통해 생성됩니다. 첫 번째 계산 단계에서는 구성 요소가 개별 레이어로 분할됩니다. 제 2 계산 단계에서, 레이저 빔에 의해 생성 된 경로 (벡터)는 각 층에 대해 생성된다. 재료가 산소로 오염되는 것을 피하기 위해, 상기 공정은 아르곤 또는 질소로 보호 가스 분위기 하에서 수행된다.
선택적 레이저 용융에 의해 생성되는 성분은 높은 비중 밀도 (> 99 %)를 특징으로합니다. 이는 생성 된 구성 요소의 기계적 특성이 기본 구성 요소의 기계적 특성과 대체로 일치 함을 보장합니다.
그러나 그것은 또한 생체 공학 원리에 따라 표적화되거나 제조 될 수 있으며, 선택적 밀도를 갖는 성분 인 부분 탄성 계수를 보장 할 수 있습니다. 경량 항공 우주 및 보디 임플란트에서, 이러한 선택적인 탄성은 종종 구성 요소 내에서 요구되며 종래의 방법을 사용하여 생산 될 수 없다.
기존의 공정 (주조 공정)과 비교하여 툴이나 몰드가 생략되어 (형태가없는 생산) 시장 진입 시간을 단축 할 수 있다는 사실을 레이저 용해로 특징 지워줍니다. 또 다른 장점은 기하학의 자유입니다. 성형 된 공정으로는 생산할 수 없거나 많은 노력을 기울여야 만 부품 형상을 생산할 수 있습니다. 또한 특정 구성 요소를 저장할 필요가 없기 때문에 저장 비용이 절감 될 수 있지만 필요할 때 생성됩니다.
노출 전략
레이저 파워가 높을수록 부품의 거칠기가 커지는 경향이 있습니다. 최신 플랜트 엔지니어링은 “셸 코어 원리”에 따라 밀도와 표면 품질을 제어 할 수 있습니다. 분할 된 노출은 구성 요소의 바깥 부분, 돌출부 및 고밀도 구성 요소 영역에 특정 영향을줍니다. 최적화 된 노출 전략은 품질 수준을 높이는 동시에 빌드 업 속도를 향상시킵니다. 세그먼트의 노출을 통해 구성 요소의 성능 프로필을 크게 높일 수 있습니다.
품질 측면 및 토폴로지
플랜트 제조업체는 i. 디. R. 한편으로는 오프 – 액시스 (또는 ex-situ)에서, 또는 다른 한편으로는 – 축에서 (또는 원위치에서).
클래식 off-axis 검사는 해상도가 낮고 탐지율이 낮습니다. 예를 들어 적외선에 민감한 카메라가 사용됩니다.이 카메라는 프로세스 챔버 외부에 위치합니다. 현장 외부 솔루션의 장점은 시스템과 카메라 시스템의 간단한 시스템 통합입니다. 축외 설계는 전반적인 용융 및 냉각 작동에 대한 설명을 허용합니다. 그러나 용융 조에 대한 자세한 설명은 알 수 없습니다.
On-axis / in-situ 설정 (예 : 빌드 개념의 레이저)은 감지기의 동축 배열을 기반으로합니다. 사용 된 탐지기는 레이저와 동일한 광학 장치를 사용하는 카메라와 포토 다이오드입니다. 이 동축 통합은 높은 좌표 관련 3D 해상도를 가능하게합니다. 인식 속도는 스캔 속도의 결과입니다. 1,000mm / s이면 결과는 100μm, 즉 사진을 찍은 거리입니다. 2,000 mm / s에서 값은 200 μm입니다. 동축 배열은 Schmelzbademissen이 항상 감지기의 한 지점에 초점을 맞추고 이미지 디테일이 줄어들어 샘플링 속도가 빨라질 수 있다는 이점이 있습니다. 용융 풀 특성 (용융 풀 면적 및 용융 풀 강도)에 대한 상세한 분석이 가능합니다.
방법
DMLS는 다양한 합금을 사용하여 프로토 타입을 생산 구성 요소와 동일한 재료로 만들어진 기능 하드웨어로 사용할 수 있습니다. 구성 요소가 층별로 내장되어 있기 때문에 캐스트 할 수 없거나 가공 할 수없는 유기적 기하학, 내부 특징 및 도전적인 통로를 설계 할 수 있습니다. DMLS는 견고하고 내구성있는 금속 부품을 생산하여 기능 프로토 타입 또는 최종 생산 부품으로 잘 작동합니다.
이 프로세스는 3D CAD 파일 데이터를 일반적으로 20 ~ 100 마이크로 미터 두께의 레이어로 슬라이싱하여 시작하여 각 레이어의 2D 이미지를 만듭니다. 이 파일 형식은 대부분의 레이어 기반 3D 인쇄 또는 광 조형 기술에 사용되는 업계 표준 .stl 파일입니다. 이 파일은 다양한 유형의 첨가물 제조 기계에 의해 파일이 해석되고 빌드 될 수 있도록 매개 변수, 값 및 실제 지원을 지정하는 파일 준비 소프트웨어 패키지로로드됩니다.
선택적인 레이저 용융으로, 분무 화 된 미세 금속 분말의 얇은 층은 수직 (Z) 축으로 움직이는 인덱싱 테이블에 고정 된 기판 플레이트, 일반적으로 금속에 코팅 메커니즘을 사용하여 고르게 분포됩니다. 이것은 500ppm 이하의 산소 수준에서 아르곤 또는 질소의 불활성 기체의 단단히 조절 된 대기를 함유하는 챔버 내에서 일어난다. 각 레이어가 배포되면 부품 형상의 각 2D 슬라이스가 분말을 선택적으로 용해하여 융합됩니다. 이것은 고출력 레이저 빔, 보통 수백 와트의 이터 븀 파이버 레이저로 수행됩니다. 레이저 빔은 2 개의 고주파수 스캐닝 미러를 사용하여 X 및 Y 방향으로 향하게됩니다. 레이저 에너지는 고체 금속을 형성하기 위해 입자의 완전 용융 (용접)을 허용 할만큼 충분히 강하다. 이 과정은 부품이 완성 될 때까지 레이어 후 반복됩니다.
DMLS 기계는 고출력 200 와트 Yb- 광섬유 레이저를 사용합니다. 빌드 챔버 영역 내부에는 자재 분배 플랫폼과 빌드 플랫폼이 있으며 리코 터 블레이드와 함께 새로운 가루를 건축 플랫폼 위로 이동시키는 데 사용됩니다. 이 기술은 집속 된 레이저 빔을 사용하여 금속 분말을 국부적으로 용융시킴으로써 금속 분말을 고체 부분에 용해시킵니다. 부품은 일반적으로 20 마이크로 미터 두께의 레이어를 사용하여 추가로 레이어별로 구성됩니다.
선택적 열 소결
선택적 열 소결 (SHS)은 첨가제 제조 공정의 한 유형입니다. 열가소성 열가소성 층에 열을 가하기 위해 열전 사 프린트 헤드를 사용하여 작동합니다. 레이어가 완성되면 파우더 베드가 아래로 내려 가고 자동 롤러가 모델의 다음 단면을 형성하기 위해 소결되는 새로운 재료 층을 추가합니다. SHS는 개념 평가, 적합 / 형태 및 기능 테스트를위한 저렴한 프로토 타입 제작에 가장 적합합니다. SHS는 SLS (Selective Laser Sintering)와 유사한 플라스틱 첨가제 제조 기술로서 SHS는 레이저 대신 열전달이 덜한 프린트 헤드를 사용하므로 저렴한 솔루션을 만들고 데스크톱 크기로 축소 할 수 있습니다.
선택적 레이저 용융 특성
기하학적 자유
기하학의 자유는 종래의 방법으로 기술적으로 또는 경제적으로 실현 될 수없는 복잡한 구조의 생산을 가능하게합니다. 여기에는 보석이나 기술 구성 요소에서 발생할 수있는 언더컷이 포함됩니다.
경량 구조 및 바이오 매틱
가벼운 구성 요소가 강도를 유지하면서 생산 될 수있는 개방 다공성 구조를 생산하는 것도 가능합니다. 경량 구조의 잠재력은 공정의 매우 중요한 이점으로 간주됩니다. 자연에서 생체 공학 템플릿은 뼈의 다공성 구조입니다. 일반적으로 바이오닉 접근법은 건설적인면에서 점차 중요한 역할을합니다.
재 설계 및 원 샷 접근법
어셈블리를 형성하기 위해 함께 조립되는 클래식 캐스트 또는 밀링 부품과 비교하여 한 번에 전체 조립품 또는 적어도 많은 개별 부품을 만들 수 있습니다 (원샷 기술). 어셈블리의 구성 요소 수가 감소하는 경향이 있습니다. 그런 다음 이전 건축의 재 설계에 대해 말합니다. 생성 요소는보다 쉽게 설치 될 수 있고 따라서 조립 노력은 일반적으로 감소된다.
혼합 건설 / 하이브리드 건설
SLM 공정에서의 혼합 구조 / 하이브리드 구조 하에서 부분적으로 생성 된 부품을 생산하는 것을 의미합니다. 여기서, 후속하는 SLM 공정에서 통상적으로 제조 된 제 1 영역의 평평한 표면 상에, 제 2의, 제조 된 구성 요소 영역이 구성된다. 하이브리드 구조의 이점은 SLM 프로세스에 의해 생성되는 구성 볼륨이 크게 감소 될 수 있고 SLM 프로세스를 통해 기하학적으로 더 까다로운 영역을 단순한 형상으로 구축 할 수 있다는 것입니다. 따라서, 금속 분말 재료의 제조 시간 및 비용은 SLM 공정 구성 요소 영역에 의해 제조되는 더 작은 체적으로 인해 감소된다.
프로토 타입 및 고유 항목
성형 공정은 금형 비용을 단위 비용으로 이전하기 위해 배치 크기가 필요합니다. SLM 프로세스는 이러한 제한을 제거합니다. 적절한시기에 샘플 또는 프로토 타입을 생성 할 수 있습니다. 또한, 틀니, 임플란트, 시계 요소 또는 보석에 요구되는 매우 개별적인 부품이 고유하게 발생할 수 있습니다. 특수 기능은 공간 (예 : 치과 임플란트, 엉덩이 임플란트 또는 척주지지 요소)에서 고유 한 항목을 동시에 생산하는 것입니다. 특히 환자를 위해 개별 구성 요소를 설계하고 제조하는 것이 가능해진다.
선택 밀도
통상적 인 밀링 또는 선삭 가공 부품에서, 부품의 밀도는 항상 고르게 분포된다. 레이저로 녹은 부품으로 인해 다양 할 수 있습니다. 구성 요소의 특정 영역은 강체 일 수 있고 다른 영역은 탄 성적으로 적용될 수있다. 예를 들어 벌집 구조 (생체 공학 원리)를 사용하면 구성 요소 요구 사항이 기존 기술에 비해 훨씬 더 창의적 일 수 있습니다.
기능 통합
복잡성이 높을수록 생성 프로세스가 개선됩니다. 기능을 통합 할 수 있습니다 (예 : 온도 제어 채널 또는 공기 주입기 또는 부품이 힌지 기능을 받거나 감각 도구가 구성 요소에 통합되어 있음). 이렇게 증가 된 값 구성 요소는 기존에 제조 된 구성 요소보다 더 효율적입니다.
“녹색 기술”
공장 가동 및 자원 절약 (사용 된 재료 / 폐기물 없음)에 사용되는 저에너지 소모와 같은 환경 측면은 레이저 용융의 기본 요소입니다. 오늘날 기계 기술에서도 종종 발견되는 오일이나 냉각수 배출이 없습니다. 잔류 열도 사용할 수 있습니다. 1,000W 레이저가 약 방출합니다. 4 kW의 열은 수냉 회로의 건물 서비스에서 사용할 수 있습니다. 기존 기술은 지속 가능성 측면에서 단점을 고려하여 점차 고려되고 있습니다. 레이저 용융은 또한 경량 구조, 툴 프리 생산, 분산 생산 및 “주문형”의 네 가지 특수한 측면에서 CO2 배출 감소에 기여합니다. 고효율 및 품질 기준과 결합 된 자원 보존의 결합입니다. 생성적인 제조는 이러한 추세를 충족시킬 수 있습니다.
주문형 생산
레이저 용융의 필수적인 측면은 필요에 따라 시간 및 현지 생산입니다. 이것은 예비 부품을 더 이상 저장할 필요가 없기 때문에 필요할 경우 인쇄 할 수 있기 때문에 항공기 제조업체와 같은 물류 개념을 매우 바꿀 수 있습니다. 또한 수요에 따라 항공기의 검사 시간을 단축 할 수 있습니다.
자재 사용 감소
특히 하부 재료의 전체 부분에서 밀링에 비해 현저한 효과가 있습니다. 평균적으로 순수한 구성 요소 무게와지지 구조에 대한 약 10 %의 재료 (이것은 구조에 필요한지지 구조 임)가 소비된다고 가정합니다.
기재
많은 선택 레이저 용융 (SLM) 기계는 X & Y에서 최대 400mm (15.748 인치)의 작업 공간에서 작동하며 최대 400mm (15.748 인치)까지 이동할 수 있습니다.이 공정에서 사용되는 재료 중에는 구리, 알루미늄, 스테인레스 강, 공구강, 코발트 크롬, 티타늄 및 텅스텐. 공정에서 사용되는 재료를 분무 화 된 형태 (분말 형태)로 존재해야합니다. 이 공정에 사용되는 현재 사용 가능한 합금은 17-4 및 15-5 스테인리스 강, 마레 이징 강, 코발트 크롬, 인코넬 625 및 718, 알루미늄 AlSi10Mg 및 티타늄 Ti6Al4V를 포함합니다.
선택적 레이저 용융에 사용되는 재료는 일반적으로 바인더가 포함되지 않은 표준 재료입니다. 기계 제조업체 및 재료 파트너는 사용자 (예 : EU 지침 및 제품 책임법에 따라 치과 기술 또는 의료 응용 프로그램)의 시리즈 자료를 인증합니다.
시리즈 물질은 분말 형태의 원자화에 의해 변환됩니다. 이것은 구형 입자를 만듭니다. 사용 된 입자의 최소 및 최대 직경은 사용되는 층 두께 및 달성 될 성분 품질의 함수로서 선택된다. 모든 분말 재료는 후속 공정에 100 % 재사용 할 수 있습니다. 사용하지 않은 재료로 새로 고침 할 필요가 없습니다.
재료 소비는 i입니다. 디. R은 다음과 같이 계산됩니다. 구성 요소 무게 + 10 % (10 % 추가 비용은 지원 구조로 인해 발생하며 제조 과정 후에 구성 요소와 분리되어야 함).
사용 된 재료는 예를 들면 다음과 같습니다.
스테인레스 스틸
공구강
알루미늄 및 알루미늄 합금
티타늄 및 티타늄 합금
크롬 – 코발트 – 몰리브덴 합금
청동 합금
귀금속 합금
니켈 기반의 합금
구리 합금
도예
응용 프로그램
선택적 레이저 용융 공정에 가장 적합한 애플리케이션 유형은 얇은 벽과 숨겨진 보이드 또는 채널이있는 복잡한 형상 및 구조이며 한편으로는 로우 로트 크기입니다. 장점은 엉덩이 줄기 또는 비구컵 또는 표면 지오메트리로 오세 인 구조가 강화 된 기타 정형 외과 임플란트와 같은 단일 물체를 만들기 위해 고체 및 부분적으로 형성되거나 격자 형태의 지오메트리가 함께 생성 될 수있는 하이브리드 형태를 생산할 때 얻을 수 있습니다. 선택적 레이저 용융 기술을 사용한 선구자적인 작업은 대부분 공구 가공 및 가공 표면에 대한 물리적 접근과 같은 전통적인 제조상의 제약이 부품 설계를 제한하는 우주 항공 분야의 경량 부품에 있습니다. SLM을 사용하면 폐기물을 제거하지 않고 부품을 추가 구성하여 거의 순수한 형상 구성 요소를 형성 할 수 있습니다.
이 공정은 많은 산업 분야에서 사용될 수 있습니다. 여기에는 다음이 포함됩니다.
항공 우주
자동차 공학
치과 기술 (의치, 임플란트)
의료 기술 (의료 기기, 내시경 검사, 임플란트 또는 정형 외과)
기계 공학
공작 기계 제작 (예 : 정밀 드릴 및 정밀 드릴)
공구 구성 (예 : 윤곽에 가까운 온도 제어용 인서트)
보석, 패션, 구두 또는 시계와 같은 생활 용품
프로토 타입 제작 : 신속한 프로토 타이핑
생체 설계 경량의 구성 요소 (예 : 뼈 구조를 모방 한 기술 구성 요소)
경주 용 작은 시리즈 (자동차 스포츠 및 오토바이 스포츠)
금속의 기술 구성 요소
전통적인 제조 기술은 비교적 높은 설정 비용 (예 : 금형 제작)을 가지고 있습니다. SLM은 부품 당 비용이 비싸지 만 (주로 시간 집약적이기 때문에), 생산되는 부품이 극히 적지 않은 것이 좋습니다. 예 : 오래된 기계 (예 : 빈티지 자동차)의 예비 부품 또는 임플란트와 같은 개별 제품 용.
J-2X 및 RS-25 로켓 엔진 용 니켈 합금으로 제작하기 어려운 기술을 실험하는 NASA의 마샬 우주 비행 센터 (Marshall Space Flight Center)의 테스트에 따르면이 기술로 제작 된 부품을 만들기가 어렵다는 것을 알 수 있습니다. 단조 및 밀링 부품보다 약하지만 종종 용접 점의 약점을 피할 수 있습니다.
이 기술은 항공 우주, 치과, 의료 및 기타 중소 규모의 부품, 고도로 복잡한 부품 및 직접 공구 삽입물을 제작하는 공구 산업과 같은 다양한 산업 분야의 직접 부품을 제조하는 데 사용됩니다. DMLS는 비용과 시간면에서 매우 효과적인 기술입니다. 이 기술은 신속한 프로토 타이핑, 신제품 개발 시간 단축 및 어셈블리 및 복잡한 형상을 단순화하는 비용 절감 방법으로 생산 제조에 모두 사용됩니다. 250 x 250 x 325 mm 크기의 일반적인 빌드 봉투 (예 : EOS의 EOSINT M280)와 한 번에 여러 부분을 ‘확장’할 수있는 기능을 사용하면,
중국 북서부 폴리 테크닉 대학교 (China Polytechnical University of China)는 유사한 시스템을 사용하여 항공기 용 티타늄 부품을 제작합니다. EADS 연구에 따르면이 공정을 사용하면 항공 우주 분야의 재료 및 폐기물을 줄일 수 있습니다.
2013 년 9 월 5 일에 Elon Musk는 EOS 3D 금속 프린터에서 나오는 SpaceX의 재생 냉각 식 SuperDraco 로켓 엔진 챔버 이미지를 트위터로 찍어 인코넬 초합금으로 구성되었음을 알았습니다. 놀랍게도 SpaceX는 2014 년 5 월에 SuperDraco 엔진의 비행 자격 버전이 완전하게 인쇄되고 처음으로 완전히 인쇄 된 로켓 엔진이라고 발표했습니다. 직접 금속 레이저 소결에 의해 추가로 제조 된 니켈과 철의 합금 인 인코넬 (Inconel)을 사용하여 엔진은 매우 높은 온도에서 6,900 킬로 파스칼 (1,000 psi)의 챔버 압력에서 작동합니다. 엔진은 엔진 고장시 고장 전파를 방지하기 위해 DMLS 인쇄 된 인쇄 된 보호 캡에 포함되어 있습니다. 엔진은 2014 년 5 월에 전체 자격 시험을 마쳤으며 2018 년 4 월 첫 번째 궤도 비행을 준비 할 예정입니다.
복잡한 부품을 3D로 인쇄하는 기능은 엔진의 낮은 질량 목표를 달성하는 데 핵심이었습니다. Elon Musk에 따르면 “매우 복잡한 엔진이며 모든 냉각 채널, 인젝터 헤드 및 스로틀 메커니즘을 형성하는 것은 매우 어려웠습니다. 매우 높은 강도의 고급 합금을 인쇄 할 수 있다는 것은 가능한 그대로 SuperDraco 엔진을 만들 수 있습니다. ” SuperDraco 엔진의 3D 인쇄 프로세스는 전통적인 주조 부품과 비교하여 리드 타임을 획기적으로 줄여 주며 “우수한 강도, 연성 및 내파 단성을 갖추고 재료 특성의 변동성이 적습니다.”
산업 어플리케이션
항공 우주 – 특정 항공 기기를 보유하고있는 에어 덕트, 고정 장치 또는 장착 장치 인 레이저 소결은 상업용 및 군사용 항공 우주의 요구 사항에 모두 부합합니다.
제조 – 레이저 소결은 적은 비용으로 경쟁력있는 비용으로 틈새 시장을 지원할 수 있습니다. 레이저 소결은 규모의 경제와 무관하므로 배치 크기 최적화에 집중할 수 있습니다.
의료 – 의료 기기는 복잡하고 가치가 높은 제품입니다. 고객 요구 사항을 정확하게 충족시켜야합니다. 이러한 요구 사항은 운영자의 개인 취향에서 비롯되는 것이 아닙니다. 법적 요구 사항 또는 지역마다 다른 표준을 준수해야합니다. 이것은 다양성의 다양성을 가져오고 따라서 변종의 작은 볼륨을 제공합니다.
프로토 타이핑 – 레이저 소결은 설계 및 기능 프로토 타입을 제공함으로써 도움을 줄 수 있습니다. 결과적으로 기능 테스트는 신속하고 유연하게 시작할 수 있습니다. 동시에, 이러한 프로토 타입은 잠재 고객 수용을 측정하는 데 사용될 수 있습니다.
공구 작업 – 직접 프로세스는 공구 경로 생성 및 EDM과 같은 여러 가공 프로세스를 제거합니다. 하룻밤 또는 심지어 몇 시간 만에 공구 삽입물이 제작됩니다. 또한 설계의 자유는 예를 들어 등각 냉각 채널을 공구에 통합하여 공구 성능을 최적화하는 데 사용할 수 있습니다.
기타 응용 프로그램
구멍이있는 부품, 언더컷, 구배 각도
맞춤, 형식 및 함수 모델
공구, 치공구 및 치구
등각 냉각 채널
로터 및 임펠러
복잡한 브라켓 팅
가능성
선택적 레이저 용융 또는 첨가제 제조 (때로는 고속 제조 또는 고속 프로토 타이핑이라고 함)는 기술을 사용하는 기술자가 고도로 숙련되어 있지만 금속 가공, 주조 또는 단조와 같은 기존 방법과 비교하여 비교적 적은 사용자로 초기 단계에 있습니다 . 임의의 공정 또는 방법과 마찬가지로, 선택적 레이저 용융은 현재의 작업에 적합해야한다. 항공 우주 또는 의료 정형 외과와 같은 시장은 기술을 제조 공정으로 평가 해 왔습니다. 수용에 대한 장벽이 높고 규정 준수 문제로 인해 인증 및 자격 인증 기간이 길어집니다. 이는 경쟁 시스템의 성능을 측정 할 수있는 완전히 형성 된 국제 표준이 없기 때문에 입증됩니다. 해당 표준은 첨가제 제조 기술에 대한 ASTM F2792-10 표준 용어입니다.
선택적 레이저 소결 (SLS)과의 차이점
SLS의 사용은 금속뿐만 아니라 플라스틱, 유리 및 세라믹과 같은 다양한 재료에 적용되는 공정을 의미합니다. SLS를 다른 3D 인쇄 공정과 차별화시키는 것은 분말을 완전히 녹이는 능력이 부족하여 분말 입자가 융합 될 수있는 특정 지점까지 가열하여 재료의 다공성을 제어 할 수있게하는 것입니다. 반면에 SLM은 금속을 완전히 녹이기 위해 레이저를 사용하여 SLS보다 한 걸음 더 나아갈 수 있습니다. 즉, 분말은 서로 융합되지 않고 실제로 입자가 균일해질 정도로 오래 액상화됩니다. 따라서 SLM은 다공성이 감소하고 결정 구조에 대한 제어력이 강해 부품 고장을 방지하는 데 도움이되는 강력한 부품을 생산할 수 있습니다. 그러나 SLM은 단일 금속 분말을 사용할 때만 가능합니다.
은혜
DMLS는 전통적인 제조 기술에 비해 많은 이점을 가지고 있습니다. 고유 한 부품을 신속하게 생산할 수있는 능력은 특별한 툴링이 필요 없으며 몇 시간 안에 부품을 제작할 수 있기 때문에 가장 분명합니다. 또한 DMLS를 사용하면 프로토 타입을보다 엄격하게 테스트 할 수 있습니다. DMLS는 대부분의 합금을 사용할 수 있기 때문에 프로토 타입은 이제 생산 구성 요소와 동일한 재료로 만들어진 기능적 하드웨어가 될 수 있습니다.
DMLS는 또한 생산에 사용되는 몇 가지 첨가제 제조 기술 중 하나입니다. 구성 요소가 레이어별로 레이어로 만들어지기 때문에 캐스팅하거나 가공 할 수없는 내부 피쳐 및 구절을 디자인 할 수 있습니다. 여러 구성 요소가있는 복잡한 형상 및 조립품을 더 적은 비용으로 간단하게 조립할 수 있으므로 비용 효율적인 조립이 가능합니다. DMLS는 주물과 같은 특수 공구를 필요로하지 않으므로 짧은 생산 작업에 편리합니다.
제약 조건
크기, 피처 세부 사항 및 표면 마감의 측면뿐만 아니라 Z 축의 오류를 통한 인쇄는 기술을 사용하기 전에 고려해야 할 요소 일 수 있습니다. 그러나 재료가 배치 될 때 x 축과 y 축에 대부분의 피처가 구축되는 기계에서 빌드를 계획함으로써 형상 공차를 잘 관리 할 수 있습니다. 표면은 일반적으로 거울이나 매우 매끄러운 마감을 얻기 위해 연마되어야합니다.
생산 툴링의 경우 최종 부품 또는 인서트의 재료 밀도를 사용 전에 해결해야합니다. 예를 들어 사출 성형 인서트의 경우 표면 결함으로 인해 플라스틱 부품에 결함이 생기며 인서트는 문제를 방지하기 위해 온도와 표면이있는 금형 밑면과 짝을 이루어야합니다.
사용 된 재료 시스템과는 별도로, DMLS 공정은 “분말 입자 크기, 층별 건축 순서 및 [분말 분배 메커니즘에 의한 소결 전 금속 분말의 확산”으로 인해 거친 표면 마감을 남긴다.
생성 된 부품의 금속지지 구조 제거 및 후 처리는 시간 소모적 인 프로세스 일 수 있으며 RP 기계가 제공하는 것과 동일한 수준의 정확도를 갖는 가공, EDM 및 / 또는 연삭 기계의 사용을 필요로합니다.
DMLS로 생산 된 부품의 얕은 표면 용융을 통한 레이저 연마는 고속 이동 레이저 빔을 사용하여 표면 거칠기를 감소시킬 수 있습니다. “표면 피크의 용융을 일으키는 데 충분한 열 에너지를 제공합니다. 용융 된 물질은 표면으로 흐릅니다. 표면 장력, 중력 및 레이저 압력에 의한 골짜기로 인해 거칠기가 감소합니다. ”
신속한 프로토 타이핑 기계를 사용할 때, 원시 메시 데이터를 포함하지 않는 .stl 파일 (Solid Works, CATIA 또는 다른 주요 CAD 프로그램에서 생성)은 .cli 및 .sli 파일로 변환해야합니다 비 조형 비 가공 기계). Software.stl 파일을 .sli 파일로 변환하면 나머지 단계와 마찬가지로이 단계와 관련된 비용이 발생할 수 있습니다.
기계 구성 요소
DMLS 기계의 일반적인 구성 요소에는 레이저, 롤러, 소결 피스톤, 제거 가능한 빌드 플레이트, 공급 분말, 공급 피스톤 및 광학 및 거울이 포함됩니다.
NAVER 학술정보 > 선택적 레이저 용융 3D 프린팅 공정과 친환경적 후처리 방식으로 제작한 초소수성 금속표면
초록
금속소재의 응용분야 확대 및 표면의 기능성 강화를 위해 적심성을 조절하는 것은 중요한 과제이다. 물방울이 바 닥 면과 이루는 각인 접촉 각은 적심성을 평가하는 척도로 친수성, 소수성 표면으로 구분한다. 초소수성 (Superhydrophobic) 표면은 소수성이 극대화 되어 물방울이 바닥 면과 150°이상의 접촉 각을 가진다. 이러한 특성 은 주로 표면에 물리, 화학적인 공정을 통해 구현되고 있다. 그러나 평판이 아닌 복잡한 형상이나 곡면 전체에 적 용하기에는 어려움이 있다. 따라서 형상에 제한이 거의 없는 선택적 레이저 용융(Selective Laser Melting, SLM)방식 의 금속 3D 프린팅 공정을 도입하여 소수성을 띄는 금속표면 제작을 하였다. 본 연구에서는 SLM 방식으로 공구강 분말을 이용해 금속표면을 제작하였다. 제작한 금속표면에 무독성의 실리콘 오일 처리와 후열처리 처리를 통해 초 소수성 표면을 구현하였다. 수백 마이크로 크기의 선 폭을 가진 패턴은 물리적으로 금속표면이 물방울과 접촉하는 면적을 줄이고 후처리 공정에서 표면에 소수성을 부여하여 물방울이 표면에서 구형에 가까운 형상이 되도록 하여 초소수성 표면을 제작 하였다. 공정 전후로 3D 프린팅 부품의 적심성 변화는 접촉 각 측정으로 평가하였다. 측정 결과로 얻은 최적의 패턴 형상과 선 폭은 곡면이나 구형의 복잡한 형상에 도입할 수 있는 가능성을 제시하였다.
산업용 선택적 레이저 용융 SLM 3D 프린터 및 서비스 및 소프트웨어
우리는 콘텐츠 및 광고를 개인 설정하고 소셜 미디어 기능을 제공하며 트래픽을 분석하기 위해 쿠키를 사용하며 소셜 미디어, 광고 및 분석 파트너와 사이트 사용에 대한 정보도 공유합니다. 개인 정보 취급 방침
[논문]선택적 레이저 용융 방법으로 제작한 치과용 코발트 크롬 합금에 대한 문헌고찰
초록
코발트-크롬 합금은 다양한 치과보철물 제작에 이용되고 있고, 다른 합금에 비해 저렴한 가격과 우수한 기계적 특성이 장점이다. 최근, 기존 제작 방식의 단점을 극복하기 위해 적층제조 방식인 선택적 레이저 용융 방법이 보철물 제작에 이용되고 있다. 선택적 레이저 용융 방법의 공정 중 급속 가열과 냉각 과정은 제작된 합금의 미세구조와 결정립을 미세화하고, 기포를 감소시켜 기존 제작 방식에 의한 합금에 비해 기계적 특성을 향상시킨다. 반면, 적층과 급속 가열 및 냉각은 다량의 잔류응력 축적을 초래하는데, 추후 기계적 특성에 악영향을 미칠 수 있다. 따라서, 잔류응력을 제거하기 위해 주로 열처리를 시행하고, 회복과 재결정화에 의한 잔류응력의 감소뿐만 아니라 상변태, 석출물 및 미세구조의 균질화가 동반되어 기계적 특성의 복잡한 변화가 나타난다. 본 문헌고찰에서 코발트-크롬 합금의 제작 방식 비교 및 선택적 레이저 용융 방법으로 제작된 합금의 특징에 대해 알아보고자 한다.
키워드에 대한 정보 선택적 레이저 용융
다음은 Bing에서 선택적 레이저 용융 주제에 대한 검색 결과입니다. 필요한 경우 더 읽을 수 있습니다.
이 기사는 인터넷의 다양한 출처에서 편집되었습니다. 이 기사가 유용했기를 바랍니다. 이 기사가 유용하다고 생각되면 공유하십시오. 매우 감사합니다!
사람들이 주제에 대해 자주 검색하는 키워드 Laser 3d sls
- 동영상
- 공유
- 카메라폰
- 동영상폰
- 무료
- 올리기
Laser #3d #sls
YouTube에서 선택적 레이저 용융 주제의 다른 동영상 보기
주제에 대한 기사를 시청해 주셔서 감사합니다 Laser 3d sls | 선택적 레이저 용융, 이 기사가 유용하다고 생각되면 공유하십시오, 매우 감사합니다.